это… Карбон: описание, сфера применения, особенности и отзывы
Передовые технологии на сегодняшний день регулярно вносят в нашу жизнь множество различных новинок, способных значительно упростить ее или же повысить ее качество. В особенности это касается создания новейших разработок химической промышленности, продукты которой находят свое применение практически в каждой отрасли человеческой деятельности. Одним из таких ноу-хау сейчас является материал карбон. О нем мы и поговорим максимально подробно в статье.
Определение
Карбон — это по своей сути углепластик, то есть композиционный, имеющий иного слоев материал. Проще говоря, углеродные волокна в виде полотна, оболочка которого, в свою очередь, выполнена из термореактивных, полимерных смол. Собственно, карбон — это сегодня почти все композитные материалы, несущая основа которых представлена в форме волокон углерода. Однако при этом связующими элементами могут быть разные вспомогательные составляющие.
Стоимость
Карбон- это очень дорогостоящий конечный продукт, стоимость которого определена внушительной долей ручного труда и сложным в целом техническим процессом. Чтобы понять, насколько дорог карбон, сравним его себестоимость со сталью. Так, если один килограмм стали обойдется производителю примерно в 1 доллар, то такой же вес карбона в 20 раз дороже. Снизить же себестоимость углепластика можно лишь путем внедрения полной автоматизации процесса его создания.
Сфера применения
Изначально карбон — это материал, который создавался для космических аппаратов и автомобилестроения. Однако со временем благодаря своим уникальным эксплуатационным показателям (малый удельный вес, высокая прочность) он нашел применение и в других сферах таких, как:
— Самолетостроение.
— Изготовление разнообразного спортивного инвентаря, удочек для рыбной ловли, шлемов.
— Производство медицинской техники и прочее.
Особые свойства
Изучая, что такое карбон отметим его основные позитивные качества. Изделия из этого материала можно формовать практически в любой конфигурации. А все потому, что углеродное полотно обладает очень высокой гибкостью, обеспечивающей, в свою очередь, оптимальный раскрой и резку. При этом следует обязательно пропитать готовый продукт эпоксидной смолой. Полученные таким образом изделия можно без проблем шлифовать, полировать, красить и даже наносить на них флексопечать.
Отличительные особенности
Продолжая рассматривать, что такое карбон (karbon) укажем его уникальные характеристики. Для всех видов этого углепластика общим является применение армирующего элемента — углеродных волокон, толщина которых находится в пределах 0,005-0,01 миллиметра, прекрасно работающих на растяжение, но не переносящие изгиб и кручение. Именно поэтому карбон- это материал, который эксплуатируют в виде полотна.Для дополнительного армирования очень часто используют каучук, который и придает углепластику серый оттенок.В целом же, карбон характеризуется износостойкостью, прочностью, жесткостью и малым удельным весом. Плотность его составляет от 1450 кг/м куб. до 2000 кг/м куб.
Тонкости технологии изготовления
Волокна из нитей углерода получают на воздухе в процессе термической обработки. То есть происходит окисление органических или полимерных нитей на протяжении суток при температуре 250 градусов Цельсия. Затем проводится карбонизация — нагревание полученных волокон в среде инертного газа в температурном диапазоне 800-1500 градусов для подготовки молекулярной структуры к оптимальной. Далее следует графитизация в этой же среде, но уже при температуре до 3000 градусов. Данный процесс может повториться несколько раз для повышения концентрации углерода до 99%.
Форма выпуска
Волокна карбона могут быть как короткими, резаными, так и в виде непрерывных нитей на бобинах. Но, как уже было сказано выше, карбон обладает плохой устойчивостью к изгибу, то углеродное волокно зачастую формируют в полотно,называемое Carbon Fabric. Причем получается оно в виде разнообразных плетений: елочка, рогожка и прочее. Бывает, что волокна просто перехватывают до заливки смолой довольно крупными стежками.Несущей основой чаще всего являются эпоксидные смолы, в которых послойно укладываются волокна карбона. Лист толщиной 1 миллиметр содержит в основном три-четыре таких слоя.
Достоинства
Карбон обладает целым спектром неоспоримых преимуществ, среди которых следует указать:
— Малый удельный вес. Даже алюминий тяжелее описываемого материала на 20%.
— Карбон, сочетающий в себе углерод и кевлар, лишь чуть-чуть тяжелее аналога с резиной, однако гораздо прочнее, а под воздействием ударной нагрузки лишь крошится, но не разлетается на мелкие частицы.
— Устойчив к высоким температурам. Карбон выдерживает до 2000 градусов Цельсия.- имеет хорошую теплоемкость и отлично гасит вибрацию.
— Устойчив к явлению коррозии.
— Имеет высокий предел упругости и предел прочности на разрыв.
— Обладает эстетичным внешним видом и декоративностью.
Недостатки
Вместе с тем карбон по сравнению с металлическими изделиями отличается таким негативными качествами:
— Высокой чувствительностью к точечным резким ударам.
— Сложностью реставрации при возникновении сколов, сломов и различных царапин.
— Выгоранием и выцветанием под воздействием ярких солнечных лучей. Именно поэтому все вещи из карбона специально покрывают лаком или же эмалью.
— Достаточно длительным производством изделий, требующим значительных затрат времени.
— Проблемами с утилизацией и повторным использованием. В зонах непосредственного контакта с металлом начинается его коррозия, поэтому в данных точках закрепляют специальные вставки из стекловолокна.
Мнение пользователей
В заключение отметим отзывы людей об описываемом в статье продукте промышленности. Итак, что такое карбон? Материал этот, как утверждают многие пользователи, очень хорош благодаря своей прочности, но при этом легкости. В особенности это оценили рыбаки, которые уже давно пользуются удочками, в основе многих из которых лежит именно карбон. Само собой, помимо этого, такие удочки еще хороши и тем, что они обладают большой долговечностью, ведь они еще характеризуются и повышенной износостойкостью.
Отделяем факты от вымысла / Велоиндустрия / Twentysix
Внутри первая часть перевода свежей статьи Ричарда Каннингема с розового ресурса про карбоний и люминий и их плюсы с неплюсами.

Недавно возник спор, где адепты алюминия утверждали, что алюминий хорошо зарекомендовал себя и благодаря переработке отходов он гораздо меньше вредит окружающей среде, чем производство карбонового волокна. Видимо кто-то считает, что где-то в Азии злые дядьки заставляют детей работать с токсическими веществами для производства карбона, чтобы какой-то чувак смог снять 2 секунды со своего любимого участка в Strava. Интересная теория, но маловероятная.
Я побывал в шкуре производителя, напрямую работал с заводами в Азии, а в качестве журналиста посетил многие заводы, которые выпускают рамы и компоненты из обоих материалов. Как и во всех спорных вопросах, правда находится где-то посередине, и сегодня мы постараемся сравнить преимущества и недостатки изготовления рам из алюминия или карбона.
«Можно ли считать покупку велосипеда непредумышленным финансированием производителя, который разграбляет земные ресурсы и наносит вред экологии?»
Если вы купили новый байк, то правильный ответ будет «да».

Но это только начало, ещё же есть выбросы из-за средств транспортировки, которыми доставляют эти материалы до производства. Трансконтинентальные трубопроводы, экскаваторы, поезда, грузовики, сухогрузы и нефтяные танкеры перемещают сырье до предприятия и попутно «гадят» в окружающую среду.
Добавьте ко всему этому загрязнения от литейных, нефтеперерабатывающих и химических заводов, которые превращают сырье в пригодные для использования формы, а затем добавьте к этому то, что места производства металла, пластика и карбонового волокна, скорее всего, находятся на другом континенте от места производства велосипеда.
Как только эти материалы будут готовы, армия контейнерных судов повезет их по всему земному шару, выгружая алюминий, карбон, сталь и полипропилен в места, где производятся рамы и велосипедные компоненты.

«Раньше я работал водителем самосвала на медном руднике, добыча там велась открытым способом. Алюминий добывают примерно так же. Так вот, мой самосвал использовал 3200 литров дизеля за одну смену, а у шахты было 92 самосвала. Работали на них две 12-часовые смены. Мы все виноваты, не важно, рассматриваете вы только производство или только добычу материалов.»
Алюминий
Перерабатывается? Да! Мало вредит окружающей среде? Не совсем.
Алюминий – самый распространённый металл на Земле и отделяется от бокситовой руды путём электролиза. Активно перерабатывается из вторсырья и используется повторно. Любые алюминиевые изделия, вроде рам, шатунов и тд, могут быть переработаны и повторно использоваться для производства, это плюс.

«Первичное производство алюминия требует огромной энергии. При этом образуются парниковые газы, которые влияют на глобальное потепление. По данным Международного Алюминиевого института, производство новых запасов алюминия приводит к выбросу 1% от общемировых выбросов парниковых газов, вызванных Человеком» — Уильям Харрис, «Как создают алюминий».
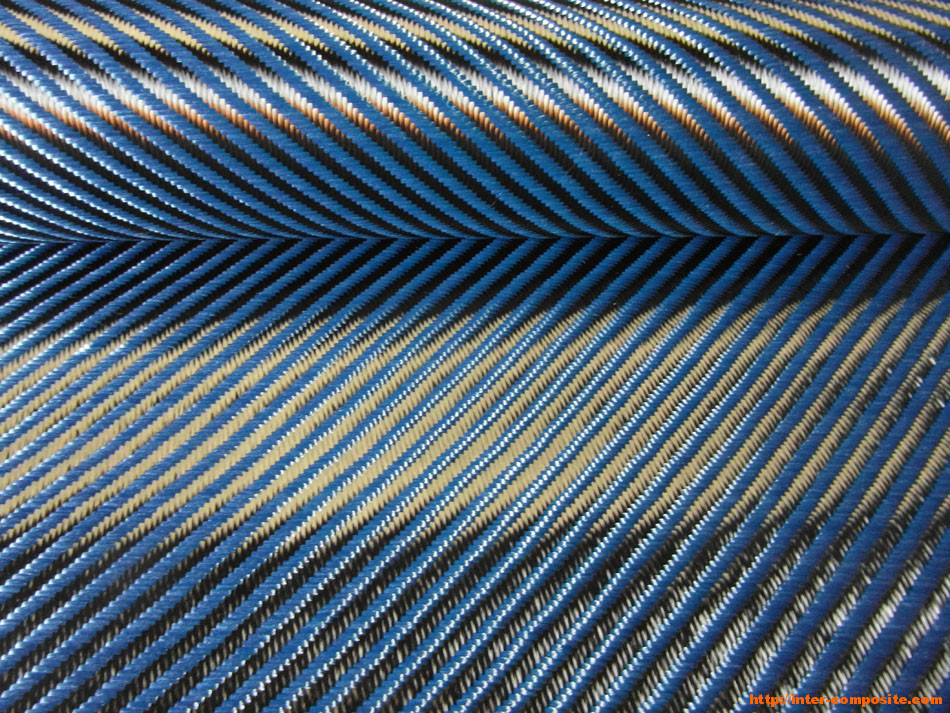
Статистика
Но судя из мировой статистики, велосипедная индустрия занимает лишь малую долю в потреблении алюминия. Мировое производство оценивается в 24.8 млн. тонн в год. Основные запасы идут на производство алюминиевых банок (187 миллиардов штук), строительное и промышленное использование, автомобили (которые в среднем используют 150 кг на единицу), аэрокосмическую промышленность. И много металла добавляется в этот плавильный котёл каждый год, а ещё больше могло бы быть переработано.
Производство рам из Алюминия
Если вы расплавите раму, весом 2.5 кг, то блок алюминия будет размером с половину листа А4 и толщиной всего в 2.5 сантиметра. Только осознайте насколько это мало, а производители умудряются уместить между задней осью и рулевой всякие шарниры и линки, крепления для аморта и прочие ништяки. Вот почему, не считая некоторых исключений, алюминиевые рамы свариваются из разных кусочков, изготовленных предварительно.
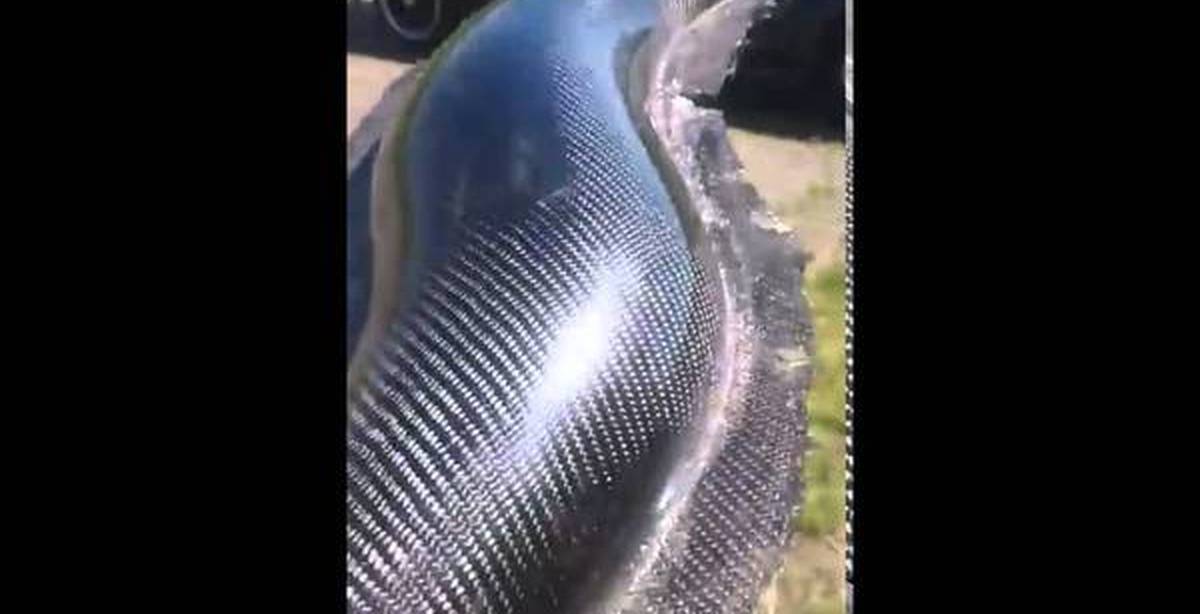
«Карбоновая рама – хорошая возможность сэкономить 200-300 грамм веса. Но только тогда, когда у вас есть подходящий дизайн, хороший производитель и опыт в постройке рам. На наш взгляд, недостаточно просто скинуть вес, нужно сохранить жесткость. До сих пор, никто из производителей карбоновых рам не превзошел наших показателей рамы Liteville в соотношении жесткости к весу». – Натаниел Гойни, отдел исследования и разработки Syntace/Liteville
Алюминию легко придать форму, и он легко подвергается механической обработке. Поэтому, чтобы оптимизировать производство и оптимизировать расходы, а также для лучшего соотношения прочности к весу рамы, используются несколько различных процессов для превращения этого 2.5 килограммового блока алюминия в раму.
Узлы, испытывающие повышенные нагрузки, вроде линков, дропаутов, стаканов и креплений для аморта, часто фрезеруются. Кареточный стакан и линки (если в них есть резьбы) дополнительно обрабатываются на ЧПУ.

Чтобы добиться максимальной прочности и минимального веса трубы изготавливаются при помощи гидроформинга, который позволяет иметь переменную толщину стенок, тем самым добиваясь усиления там, где это необходимо.
Сварка этих частей вместе создает цельную структуру (раму), которую нельзя сделать, используя какой-то один метод. Каждая рама должна быть дополнительно термообработана после сварки и пройти проверку качества.
ТИГовая сварка переднего треугольника на фабрике Intense. Для каждого размера рамы используются свои трубы, и они должны идеально совпадать друг с другом.
Сварные рамы должны быть правильно собраны на стапеле, сварены и термообработаны.
Использование лучших методов для создания ключевых компонентов, а затем сварка их вместе приводит к минимальному количеству отходов и является основной причиной того, что алюминий является конкурентоспособным по соотношению цена/качество.

Есть ли способ сделать раму лучше? Pole Bicycle Company (PBC) предлагают использовать ЧПУ для производства из цельных кусков алюминия. Чтобы сделать легкую трубчатую структуру, раму предлагают делать из половинок, а потом соединять их вместе. Успешным примером этой технологии являются шатуны Cannondale Hollowgram. Сейчас у PBC есть проект рамы, сделанной по такой технологии, с весом 3.2 кг без амортизатора.
(Как я понимаю, половинки рамы предлагают скручивать вместе/ Переводчик).
«7075 T6 алюминий в 1.7 раз прочнее обычного 6061 T6. Это позволяет изготовить сделать раму легче, чем обычные алюминиевые рамы. Раму делают из высококачественных заготовок, используемых в аэрокосмической промышленности, а термообработка гораздо лучше, чем термообработка обычных рам в духовке (т.к. не используется сварка и нет мест с напряжениями/ Переводчик)».

Если предположить, что в PBC будут использованы брусы алюминия толщиной в 2.5 см, и технологически возможно сделать достаточно крепкую раму весом 2.5 кг, то на производство каждой рамы уйдет до 50 килограмм алюминия (примерный расчет). Более крупные обрезки брусов можно использовать повторно, но львиная доля станет металлической стружкой и отправится в утиль. Дизайнер PBC Лео Кокконен неохотно обсуждал эти цифры: « Процесс обработки нашей рамы является коммерческой тайной, поэтому, к сожалению, я не могу подтвердить какие-либо ваши цифры о размерах заготовок. Я могу сказать, что у нас есть способы сохранить материал при механической обработке.»
Перспективна ли возможность производства рам из брусов алюминия? Возможно для «бутиковых» производителей. Но, по моим подсчетам, для производства 1000 рам пришлось бы импортировать 50 тонн алюминия, а потом отправить 43 тонны в утиль на переработку.
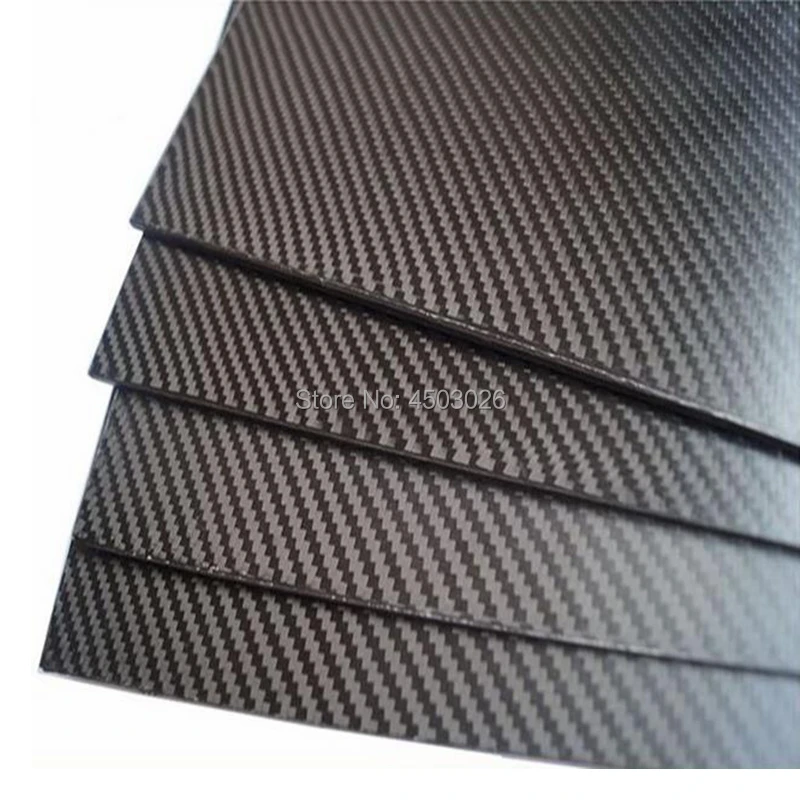
Завод Genio, Тайвань: большая часть трудозатрат для производства алюминиевой рамы уходит на подготовку деталей для сварщиков, которые творят магию.
Обратной стороной производства алюминиевых рам «традиционным» способом является огромное количество производственных процессов. На каждом этапе есть хотя бы одна специальная машина, требующая обученного оператора, которых мало.
Металлообработка — это опасное занятие. Как правило, на каждом этапе есть защитные механизмы, но ЧПУ, кузнечные прессы, экструзионные машины, трубогибочные станки, промышленные лазеры, отрезные пилы и печи для термообработки могут нанести серьезный вред человеку.
Для обработки алюминия требуется ряд химических процессов для очистки, сварки, смазки, термической обработки, окраски и анодирования, и многие из этих процессов происходят под одной крышей.
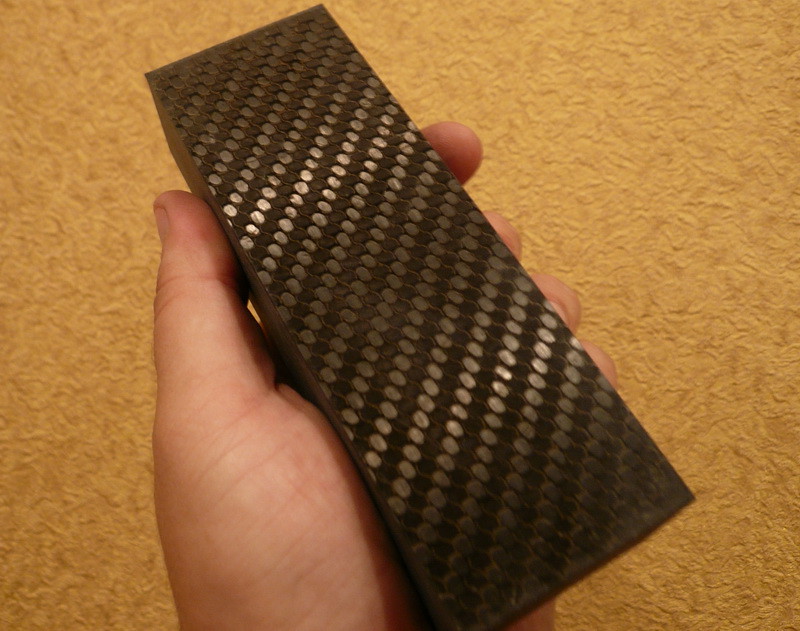
Каждый завод, который я посетил, хорошо проветривался, но на нём присутствовала своя «атмосфера». Даже когда существуют значительные меры предосторожности, мой опыт показывает, что каждый работник в какой-то степени подвергается воздействию побочных продуктов производства.
Очистка и предварительная подготовка алюминиевых рам. Химическое воздействие на организм человека присутствует на всех этапах производства.
Если бы вам пришлось год проработать на заводе, где делают алюминиевые рамы, и год на заводе, где делают карбоновые, какой бы вы в итоге выбрали?
«Я бы выбрал завод с алюминиевыми рамами. Мне нравится работать с металлом и вымазывать руки, а не носить резиновые перчатки и респиратор». – Натаниел Гойни, отдел исследования и разработки Syntace/Liteville. (Еще бы он сказал что-то другое, работая в фирме, которая делает Алю рамы/ Переводчик).
Переработка Алюминия
Переработка алюминия даёт примерно 95% сокращение энергозатрат на конечном продукте (если сравнивать с процессом добычи из Боксита).
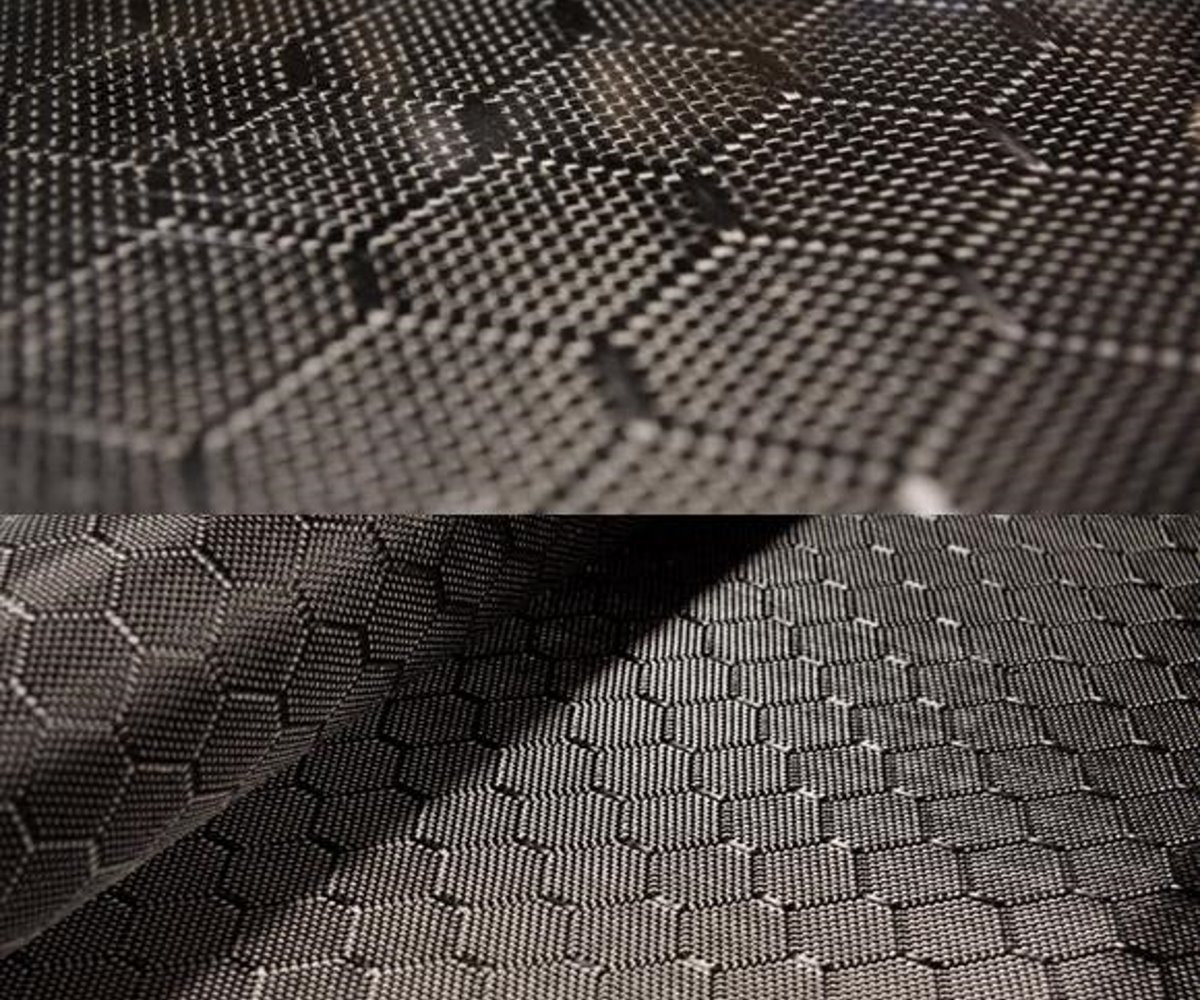
Утилизация алюминия началась из-за его недостатка во время Второй мировой войны. Однако, после того как в обиход вошли алюминиевые банки с газировкой, ими быстро загадили окружающую среду, многие государства стали стимулировать утилизацию. Ведь банка – это чистый алюминий и источник премиум-сырья для литейных цехов, которые производят высокопрочные сплавы. Причина, по которой переработка алюминия настолько распространена в развитых странах, это низкие налоги и квоты на такие производства, ну и, конечно то, что люди очень сильно мусорят.
Куча алюминиевых банок может стоить дороже, чем ваша рама.
Алюминиевый лом делят на две основные группы. Первая – это «чистый» алюминий, который не загрязнен краской или другими не алюминиевыми веществами. Большая часть такого лома приходит с предприятий по обработке или производству.

«Грязный» алюминий – это либо неизвестный сплав, либо любой алюминий, который был окрашен, или смешивается с другими металлами. Блок двигателя, складная лестница, Airbus A320s и велосипедные рамы из этой категории. Это наименее желанный материал, поскольку требуют гораздо большего труда и энергии для очистки, а процесс переработки более токсичен и дает больше отходов.
В Калифорнии вы получите в среднем 4 доллара за 1кг алюминиевых банок (плюс субсидия $0.05), за чистый алюминий вам дадут $1.55, а за грязный $0.90.
После звонков по крупным и средним велосипедным брендам я убедился, что почти на каждом заводе есть программа утилизации. Однако, после продажи, эти рамы находятся далеко-далеко от плавильных печей. Люди всё ещё перепродают и используют рамы, построенные в 1980 году.
Однако, если вы решили, что ваша рама Commencal Supreme DH уже отслужила своё, то можно не продавать её кому-то на барахолке, а переработать.

На этом алюминиевая часть заканчивается и начинается карбониевая, но о ней вы узнаете в следующем посте, т.к. что-то слишком много чтива получилось.
Отделяем факты от вымысла. Часть 2 / Велоиндустрия / Twentysix
Вторая часть нашумевшей статьи. Love or hate! На фото выше – рама Unno в готовом виде на фоне всех лоскутов карбонового волокна, которые в ней были использованы.
Карбон
Практически непригоден для переработки, но и отходов меньше.
Откуда взялся
Из названия (Карбон ака углерод) понятно, что это продукт переработки сырой нефти. Если просто описать процесс, то из Акрила (полимер на основе акриловой и метакриловой кислот, не путать с оргстеклом/ Переводчик) сначала делают синтетическое волокно, за этим следует 3 стадии термической обработки:
Первая – окисление исходного волокна на воздухе при температуре 250 °C в течение 24 часов.
Вторая – нагрев в инертной (азот/аргон) при температурах от 800 до 1500 °C.
Третья – термическая обработка в инертной среде при температуре 1600-3000 °C.
В результате всех этих хитрых манипуляций получается волокно с содержанием углерода около 99% от общего количества. Это весьма сложный и дорогостоящий процесс. Машины, которые плетут такое волокно, очень длинные и их немного, что сказывается на конечной стоимости продукта. А вот уже готовые нити можно скатывать в мотки и хранить сколь угодно длительное время, так как сам материал инертен. Изготовить из такой нити лоскут ткани не сложнее, чем производство любой другой текстильной продукции.
Производственная линия в Oak Ridge длиной 120 метров (в начале 40-х в этом городе ковался ядерный щит США, под кодовым названием «Манхеттенский проект». Именно там родились бомбуэ, упавшие на Хиросиму и Нагасаки/ Переводчик).
Но после того, как из нитей сплетут какое-то изделие, зальют его смолой и запекут в печи, их очень трудно переработать. Смолы, которыми фиксируются волокна, при разложении токсичны, а основным методом переработки является измельчение углеродного материала (банально дробят и жгут готовые продукты/ Переводчик). Понятно, что после такой «переработки» о повторном использовании в качестве материала для исходного изделия даже не идёт речь. Вероятность того, что карбоновая рама после переработки снова будет карбоновой рамой – крайне мала.
Статистика
Глобальный объем производства карбонового волокна около 135 000 тонн в год (сравните с 24 800 000 тонн алюминия). На 2017 год крупнейшими производителями были США и Мексика (48.7 тыс. тонн), Япония (27.1 тыс. тонн) и Китай (13.3 тыс. тонн). Аэрокосмическая отрасль потребляет около 80% от общего оборота (в среднем на один самолёт Boeing/Airbus уходит до 30 тонн/ Переводчик), 15% занимают производители спорттоваров, где лидирующие позиции занимает гольф (!) и «лыжные» виды спорта, велосипеды пасут задних. Ожидается, что в скором времени и автомобильная промышленность тоже станет весомым игроком на рынке.
Производство карбониевых рам
Чтобы превратить нить в карбоновую раму, из неё сначала делают лоскуты ткани с однонаправленными или разнонаправленными «жилами», затем эти лоскуты ткани пропитываются смолой и складываются в определенном порядке вокруг специальной надувной формы. С момента начала пропитки смола начинает застывать и вам нужно использовать пропитанный лоскут, либо поместить его в холодильник на хранение. Лоскуты липнут друг к другу, что упрощает процесс наслаивания лоскутов вокруг формы.
Лоскуты карбона оборачивают вокруг надувной пенополистирольной формы для будущей рамы Pivot.
Предварительно подготовленные лоскуты карбоновой ткани пропитывают специальной смолой, которая не затвердеет полностью, пока её не нагреют до определенной температуры. Чтобы все лоскуты хорошенько пропитались смолой и склеились друг с другом, их помещают в специальную форму из двух скручивающихся половин, а в надувную форму, вокруг которой складывались пластины, подают газ под давлением. После всех этих процедур рама в форме отправляется в автоклав для запекания. После того, как запеченный карбон остынет, его уже нельзя будет повторно расплавить и использовать, как это делается с пластмассой.
Специальная внешняя металлическая форма для запекания.
Существует ещё несколько способов производства карбоновых конструкций, но большинство ведущих производителей используют именно этот метод. Сами формы для запекания делаются из стальных болванок. Для каждого размера рамы нужна своя подходящая форма. Передний треугольник чаще всего делают за один подход, а заковыристые детали вроде свингарма (задний треугольник или перья, кому-как угодно/ Переводчик) приходится делать из нескольких частей, соединяя их во время запекания.
Сама форма стоит от 40 000 до 80 000 долларов в зависимости от сложности конструкции (именно поэтому прототипы лепят из алюминия, с ним проще работать в плане экспериментов/ Переводчик), а живут они от 1 до 3-х лет, в зависимости от того, сколько сил потребуется для извлечения карбоновой детали после запекания.
После запекания и остывания карбоновые детали рамы Pivot извлекаются из форм.
«Если вы используете алюминий, то от момента получения материала, после обработки заготовок, ковки, и гидроформинга труб, до готовой рамы проходит 150-180 дней, а минимальный размер партии около 500 единиц. Тот же процесс для карбоновых рам составляет 90-120 дней. Алюминий дешевле, но планировать его производство сложнее». – Крис Кокалис, основатель Pivot Cycles.
Соотношение прочности к весу у карбона просто невероятно. Европейская фирма Dexcraft Composites говорит, что одна и та же деталь, с одинаковой толщиной стенок, созданная из карбона будет на 31% жестче, чем алюминиевая. При этом она будет вполовину легче и крепче на 60%. А если вы сделаете такую деталь из многослойного, разнонаправленного волокна, то показатели будут ещё выше. Шоссейные и некоторые кантрийные образцы рам уже впрямую приблизились к этим цифрам, однако производители серьезных МТВ-пушек слишком консервативно подходят к процессу создания рам и сейчас разница между алюминиевой и карбоновой рамой всего полкилограмма (то есть теоретически можно сделать даунхилльную раму, весом 2 кило, а в случае Трека вообще 1. 5/ Переводчик).
Делать карбоновые рамы гораздо проще. Им не нужны крутые сварщики и стапели для сварки, а дополнительная прочность только помогает производителям, ведь раму банально труднее сломать, а значит и менять по гарантии ничего не придётся. Персонал на заводе должен быть внимательным и осторожным, но не обязательно высококвалифицированным (ага, можно набирать работников с улицы, которые будут работать за еду, профит/ Переводчик). Обычно «поклейка» танчиков велосипеда происходит в хорошо проветриваемой комнате с кондиционером, а процесс производства гораздо менее травмоопасен.
Обратной стороной являются первоначальные затраты на материалы (от $40 за кило), и на формы для запекания для тестовых образцов. Сам процесс укладки лоскутов карбона утомительный, а делать его нужно правильно. При этом он оплачивается слабо (из-за обилия желающих поклеить за еду/ Переводчик) и опытные работники тут не задерживаются.
Несмотря на обилие токсичных веществ, уже пропитанные лоскуты редко бывают опасны для работников, а ведь большинство небольших производителей закупается уже пропитанными лоскутами. Хотя длительное воздействие на открытую кожу и может вызвать аллергическую реакцию, но резиновых перчаток вполне достаточно для защиты, плюс они помогают избежать попадания влаги, масел или грязи внутрь во время поклейки.
Более крупные производители, вроде Giant Bicycles, предпочитают пропитывать лоскуты самостоятельно, чтобы не зависеть от поставок и иметь ровно столько подготовленного материала, сколько нужно. Понятно, что персонал помещений, где происходит подготовка и пропитка карбонового волокна, подвержен повышенному риску.
Переработка карбония
В данный момент велопроизводители не создают такие объемы карбоновой продукции, чтобы по её лому были какие-то данные. Toray – один из самых больших производителей карбонового волокна, заявляет, что около 4.5 тысяч тонн карбонового лома появляется каждый год, из которого тысяча тонн приходит из Вашингтона, где Toray обслуживает Boeing и другие аэрокосмические предприятия. Из карбонового мусора от Boeing’а и компании можно делать 400 000 карбоновых велосипедов в год, но отходы велоиндустрии ничтожно малы.
Сейчас робот просверлит первое отверстие в 65-метровом крыле Боинга 777X. В нем почти 650 километров углеродной нити.
В Toray закладывают примерно 20% на отходы от производств аэрокосмической отрасли, а в велосипедной промышленности такого нет и подавно, как у мелких производителей, так и у крупных. «Мы делаем 125 ободов в неделю. И общее количество отходов от производства – это один пластиковый мешок для мусора набитый бумажной обёрткой». – говорит всё тот же Дастин Адамс.
Крупные велосипедные производители, вроде Trek, Specialized, или Ibis – отправляют на вторичную переработку те рамы, которые пришли по гарантийному возврату. Для переработки карбоновый лом выжигают в печах и дробят, а получившуюся мешанину используют для усиления пластика, изготовления структурных панелей, смешивают с асфальтом и используют для армирования бетона.
На фото хорошо видно, что тормозные ручки Magura MT8 сделаны из переработанного карбонового волокна (видимо сам рычаг по новой заливают эпоксидной смолой, а вот ручка сделана из пластика с добавлением переработанного углеродного волокна/ Переводчик).
/Дальше идёт зелёная чепуха о том, какие велопроизводители молодцы, что все отправляют отходы на переработку и сами пытаются изобрести какие-нибудь новые методы переработки, и как им приходится кооперироваться, чтобы насобирать лома на минимальную отправку и тд и тп./
А что можешь сделать ты?
Как и с алюминиевым велосипедом, свою карбоновую раму едва ли кто-то захочет отправить в утиль, ведь с заложенными характеристиками и свойствами самого карбона рама скорее морально устареет, чем сломается, а вы сможете говорить своим внукам – «Смотри, щенок, на чём твой дед виповал!»
Всё тот же Крис Кокалис говорит, что карбоновая рама даст вам максимальную прочность и минимальный вес и позволяет не так запариваться по поводу особо нагруженных узлов, как алюминиевые рамы. С другой стороны, если вы можете предложить схожую по характеристикам раму, пусть и с чуть большим весом, но по более выгодной цене (примерно на $1к меньше), то это весьма жизнеспособный вариант. За примерами далеко ходить не надо, алюминиевый Mach 6 от Pivot или тот же Specialized Demo.
Сравнение карбоновой и алюминиевой рам Specialized Demo 8.
Так что же лучше?
Если бы лично я собирался запустить новый завод по производству горных велосипедов, я бы взял карбоний. Я считаю, что алюминиевые конструкции достигли своего апогея и без каких-то новых прорывных технологий в этой сфере ничего не изменится. Логика проста, если дать по миллиону долларов на улучшение карбоновой и алюминиевой рамы, то едва ли алюминиевый вариант будет сильно отличаться от тех топовых образцов, что мы видим на рынке сейчас. А вот карбоновые технологии новы и только начали развиваться.
Если бы я учил детей в школе рациональности использования природных ресурсов, то катался бы на алюминиевом велосипеде потому, что мне бы не пришлось спорить с детьми на тему того, почему я взял карбоновый велосипед, если его очень сложно переработать.
А если бы я владел компанией, которая хочет производить велосипеды, но заботится о окружающей среде. То сначала бы разработал подходящий дизайн для рамы, а потом бы нашел хороший завод, который не сливает отходы в океан или что-то в таком духе.
Если я просто езжу эндуро или даунхилл, то не думаю, что полкило или килограмм, который я смогу сэкономить благодаря карбоновой раме и колёсам, как-то заметно повлияют на моё катание. А вот для профессионалов карбон – это отличный выбор.
А ломается всё.
//////////
В общем да, понимаю чувства тех, кто ждал срыв покровов и ответа на вопрос «Что же лучше», а получил перевод статьи про экологию, разбавленную моими комментариями и выдержками из википедии в части производства и утилизации материалов. Сильно не серчайте.
Зачем нужен карбон?
Он на 75% легче железа и на 30% — алюминия, и при этом имеет прочность на разрыв в четыре раза выше, чем у лучших марок стали.
Сами по себе карбоновые нити довольно хрупкие, поэтому из них плетут гибкие и эластичные полотнища. При добавлении к ним связующих полимерных составов получают углепластики, которые совершили настоящий переворот в спорте, технике и многих других областях человеческой деятельности.
Карбон на дорогах, в небе и на море
Наиболее широко известная область применения карбона — это автомобилестроение. Вначале его выдающееся сочетание прочности и легкости заинтересовало конструкторов болидов Формулы-1, что позволило значительно снизить вес гоночных машин. Джон Бернард, инженер британского автомобильного производителя McLaren, впервые сделал элементы кузова из углеволокна в начале 1980-х гг. Это дало столь ощутимую прибавку в скорости, что сразу привело гоночную команду McLaren на призовые места.
Впрочем, право быть самым быстрым обходится весьма недешево из-за того, что все углепластиковые детали фактически изготавливаются вручную. Карбоновую ткань особого плетения выкладывают в литейные формы, затем соединяют полимерными составами. На заключительном этапе она подвергается обработке при высокой температуре и давлении. Поэтому долгое время карбоновые элементы кузова использовались только в суперкарах и моделях премиального класса. И лишь недавно анонсирован выпуск доступных широкой аудитории серийных моделей с углепластиковыми деталями. Так, в конструкции кузова нового BMW i3 будут широко представлены элементы из углеродного волокна. А в новой версии хэтчбека Volkswagen Golf GTI VII благодаря углепластиковым капоту и крыше удалось снизить вес машины сразу на 200 кг!
Еще более широкое применение материалы на основе карбона получили в авиастроении , где они начали теснить традиционные алюминий и титан. Первыми перспективы оценили авиаконструкторы, работающие в оборонной промышленности. Например, в новейших российских истребителях Су-47 и Т-50 используются углепластиковые компоненты крыла и фюзеляжа.
Все шире применяется карбон и в пассажирских самолетах, где он позволяет снизить расход топлива и повысить грузоподъемность. Так, в лайнере Boeing 787 Dreamliner не менее 50% элементов фюзеляжа изготовлены из композитных материалов на основе углерода, благодаря чему расход топлива снижен на 20%. С той же целью самый большой пассажирский авиалайнер Airbus А380 оснастили крыльями, которые на 40% состоят из углепластиков. А фюзеляж современного бизнес-джета Hawker 4000 почти целиком изготовлен из этого материала!
Не менее активно используется карбон и в кораблестроении. Причина популярности та же: уникальное соотношение прочности и веса, жизненно важное в суровых морских условиях. Кроме того, для корабелов ценны ударопрочность и коррозионная стойкость этого материала.
Как обычно, первыми начали применять углепластики в оборонной сфере. Из карбоновых композитов делают элементы корпусов подводных лодок, поскольку они серьезно снижают шум и обладают stealth-эффектом, делая судно «невидимым» для радаров противника. А в шведских корветах типа «Visbi» корпус и надстройки сделаны из карбоновых композитов по stealth-технологии. Используется многослойный материал с основой из ПВХ, которая покрыта тканью особого плетения из углеродных жгутов. Каждый такой жгут поглощает и рассеивает радиоволны от радаров, не давая обнаружить судно.
Для гражданских кораблей невидимость для радаров не нужна, а вот легкость, прочность и возможность изготавливать детали практически любой конфигурации оказались очень востребованными. Чаще всего карбон применяют при строительстве спортивных и прогулочных яхт, где важны скоростные характеристики.
Элементы будущего судна «лепятся» из углепластиковых холстов по компьютерной модели как из пластилина. Вначале делается полноразмерный макет палубы и корпуса из специального модельного пластика. Затем по этим лекалам вручную слоями выклеиваются полотнища карбоновой ткани, скрепляемой эпоксидными смолами. После просушки готовый корпус шлифуют, красят и покрывают лаком.
Впрочем, есть и более современные способы. Например, итальянская компания Lanulfi сумела почти полностью автоматизировать процесс.
Крупные конструктивные элементы судна с помощью 3D моделирования разбивают на более мелкие, но идеально совпадающие части. По компьютерной модели с помощью станка с программным управлением выполняются основы, которые и служат матрицами для выклеивания углепластиковых деталей. Такой подход позволяет добиться максимальной точности, что очень важно для ходовых качеств спортивных яхт.
Карбон для каждого
Карбон начинает все шире применяться и в строительстве. Добавление углеродных волокон в состав бетона делает его гораздо более устойчивым к внешним воздействиям. Фактически получается сверхпрочный монолит с очень плотной поверхностью. Такая технология применяется в строительстве небоскребов и плотин, а также при обустройстве туннелей.
Стоит упомянуть и материалы для усиления, ремонта и реставрации железобетонных поверхностей — специальные холсты и пластины из карбоновой ткани (например, Mapewrap или Carboplate). Они позволяют полностью восстановить конструкцию, не прибегая к дорогостоящей и не всегда возможной перезаливке.
Для крупных девелоперов и частных застройщиков особо интересна такая инновация, как применение карбона в штукатурной системе утепления фасадов.
«Добавление в армирующий состав мельчайших карбоновых волокон диаметром менее 15 микрон приводит к очень важному результату — многократному увеличению ударопрочности фасада, — говорит Роман Рязанцев, проект-менеджер компании CAPAROL, эксперта в области защиты и теплоизоляции фасадов зданий. — В частности, карбоновая добавка в штукатурную систему CAPATECT Carbon (Caparol) позволяет фасаду без вреда переносить удары с энергией до 60 Джоулей — это в десять раз больше, чем способны выдерживать обычные варианты штукатурных фасадов».
Если владелец коттеджа решит использовать такую систему для внешней отделки своего жилища, то он не только сократит затраты на отопление и обеспечит благоприятный микроклимат в помещениях, но и защитит стены от любых механических воздействий. Крупный град разбивает виниловый сайдинг и оставляет вмятины на обычной песчаной штукатурке. Шквалистый ветер, несущий с собой мусор и ветки деревьев, также может повредить фасад. Но на отделке с добавлением карбоновых волокон не останется ни следа. Тем более не страшны ей такие бытовые воздействия, как удары мячом или шайбой в детских играх.
«Обычно для защиты цокольной части фасада от случайных повреждений используют облицовку камнем, например, керамогранитом, — отмечает Даниил Мазуров руководитель отдела оптовых продаж московской строительно-торговой компании «ПКК Интерстройтехнологии».
— Но для отделки цокольной части жилого комплекса, который сейчас строится на юге Москвы, мы решили попробовать штукатурную систему с карбоном. В сравнительных испытаниях она показывала очень впечатляющие результаты».
Вадим Пащенко, руководитель направления WDVS Московского регионального отдела компании CAPAROL, называет еще одно ценное следствие применения в штукатурной системе армирующих компонентов с карбоновыми волокнами: фасад становится устойчив к температурным деформациям. Для архитекторов и владельцев частных домов это означает полную свободу в самовыражении — можно окрасить стены дома в любые самые тёмные и насыщенные цвета. С традиционной цементно-песчаной штукатуркой такие эксперименты могут закончиться печально. Темная поверхность стены слишком быстро нагревается под солнечными лучами, что приводит к образованию трещин на внешнем защитно-декоративном слое. Но для фасадной системы с карбоновыми волокнами подобной проблемы не существует.
Сейчас по всей Европе начинают появляться выделяющиеся на общем фоне частные коттеджи и коммерческие здания, школы и детские сады, которым карбон помог обрести выразительные и насыщенные цвета. По мере того как российские частные домовладельцы начинают экспериментировать с цветами фасадов, отходя от традиционных пастельных оттенков, эта инновационная технология становится востребована и в нашей стране.
Карбон для поколения Next
Без карбона ныне невозможно представить ни одну высокотехнологичную отрасль. Он становится все доступнее и для обычных людей.
Сейчас мы можем приобрести углепластиковые лыжи, сноуборды, горные ботинки, спиннинги и велосипеды, шлемы и прочую спортивную экипировку.
Но на смену ему уже идет новое поколение материалов — углеродные нанотрубки, которые в десятки раз прочнее стали и обладают массой других ценнейших свойств.
Так, канадский производитель одежды Garrison Bespoke разработал мужской костюм, который сделан из ткани на основе углеродных нанотрубок. Такая ткань останавливает пули до сорок пятого калибра и защищает от колющих ножевых ранений. Кроме того, она на 50% легче кевлара — синтетического материала, используемого для изготовления бронежилетов. Подобные костюмы наверняка войдут в моду среди бизнесменов и политиков.
К числу самых фантастических применений карбоновых нанотрубок относится космический лифт, который позволит доставлять на орбиту грузы без дорогих и опасных запусков ракет. Его основой должен стать сверхпрочный трос, протянутый от поверхности планеты к космической станции, находящейся на геостационарной орбите на высоте 35 тыс. км над Землей.
Эта идея была предложена еще великим русским ученым Константином Циолковским в 1895 году. Но до сих пор проект казался неосуществимым по техническим причинам, ведь не было известно материалов, из которых можно сделать настолько прочный трос. Однако открытие углеродных нанотрубок в начале 1990-х гг. заставило пересмотреть границы возможного. Сотканная из карбоновых нанотрубок нить миллиметровой толщины способна выдержать нагрузку примерно 30 тонн. А значит, дешевые и безопасные путешествия на орбиту в кабине космического лифта из фантастического сюжета превращаются в практическую задачу для инженеров.
Пресс-служба CAPAROL
Технологии
Удилища из стеклопластика,графита и карбона. Как быть? | planet-watersport.ru
16 Ноября 2018, 05:14 6852
Все современные спиннинги делаются полыми либо из углепластика, либо из стекловолокна, либо из их композиции (смеси). Следует помнить, что углепластик, графит, карбон — это одно и то же. Удилища из стеклопластика наиболее гибкие и тяжелые, с небольшим модулем упругости. Углепластиковые — самые легкие, жесткие и посылистые, с большим модулем упругости.
Но они более хрупкие, чем стеклопластиковые и требуют, соответственно, более бережного обращения. Средние по жесткости и наиболее распространенные — это удилища, сделанные из композита (к графитовым волокнам добавляются волокна из стеклоткани). Встречаются также удилища с добавлением кевлара (прочнейший материал, из которого изготавливают бронежилеты). Сегодняшние высокомодульные графитовые удилища не так прочны, как удилища, сделанные из низкомодульных волокон несколько лет тому назад. Но уменьшение прочности это не результат «хрупкости», как может показаться. Первые сорта графита, используемые для изготовления рыболовных удилищ, имели более высокую модульность, хотя и меньшую пластичность, чем стекловолокно. Однако их уровень эластичности был более чем достаточен для обеспечения адекватной прочности, и их высокий модуль упругости делает их экстремально чувствительными. На заре изготовления графитовых удилищ было тяжело достигнуть успеха даже с высокомодульными графитами потому, что при возрастании модуля упругости уменьшается пластичность. Больше углеволокна — больше жёсткость, но и хрупкость тоже, вот что предлагалось.
Но углеволокно, известное как IM6, всё изменило. У IM6 не только выросла модульность, но и пластичность тоже достаточно высока. Сразу стало возможно облегчить изделия, увеличить чувствительность удилища без потери прочности из-за хрупкости. Большинство высокомодульных графитовых волокон, используемых в бланках сегодня, имеют модульность и пластичность выше, чем IM6. Таким образом, было бы некорректно сказать, что они более хрупкие, даже при сравнении ранних графитов и стекловолокна. Всё ещё нет сомнения, что легче сломать высокомодульное графитовое удилище, чем стеклопластиковое удилище.
Но если они не более хрупкие, в чём же дело? Ответ довольно прост. Используя волокно, которое жёстче при том же весе, нет необходимости использовать столько же материала, достигая той же жёсткости, как было бы необходимо при использовании волокна меньшей модульности. Таким образом, сейчас мы имеем меньше материала в бланке, который обычно имеет при этом тонкие стенки. Более тонкие стенки не позволяют выдерживать те же нагрузки при ударе, как более толстые. Да, мы можем уменьшать диаметр и толщину стенок, но вы потеряете некоторую жесткость, поступая подобным образом и добавив больше волокна, улучшите эти … хорошо, мы просто начнём с начала до этой точки.
Установленный факт, что большинство современных высокомодульных удилищ не хрупки, но они имеют более тонкие стенки, нежели их предшественники несколько лет назад. Они разработаны для получения высочайшего уровня эксплуатационных характеристик, в то же время позволяя надеяться на адекватную прочность.
Если вы или ваши клиенты ломаете много удилищ вами сделанных и это высокомодульные удилища, скорее всего это происходит вследствие неправильного обращения с удилищем. Если не заботиться хорошо об удилище при хранении и эксплуатации, то я бы советовал опуститься к низкомодульным сериям бланков, которые лучше выдерживают удары и падения. Как и во многих других случаях, вы должны пойти на компромисс в одних характеристиках для достижения других. С очень высокомодульными удилищами вы теряете способность к падениям и ударам, но зато приобретаете более эффективный рыболовный инструмент. В другом случае, вы найдёте серии бланков, которые будут выдерживать испытания и вы должны решительно взять их, но, понимая, что это увеличение прочности будет ценой за характеристики.
Лучше вовсе отказаться от спиннингов из стекловолокна, поскольку их большой вес и сравнительно малый модуль упругости притупляют чувство проводки. Опять же вы можете мне возразить: всю жизнь ловим «стеклом» и никаких проблем! Чтобы убедиться, что проблемы все-таки есть, достаточно попробовать в деле качественный «углевый» спиннинг. Сразу бросится в глаза, насколько четче ощущается проводка, и будет гораздо меньше «слепых» поклевок.
Углепластик, при высоком его модуле, обладает и другими важными преимуществами перед «стеклом» и композитом. Возьмите произвольное удилище и встряхните его, как бы выполняя заброс. Как только движение руки остановится, вершинка спиннинга кивнет вперед и выпрямится. По тому, как это происходит, можно делать выводы о достоинствах удилища.
Если встряхивание удилища рождает несколько размашистых переколебаний, что типично для многих «стеклянных» спиннингов и некоторых графитовых, воздержитесь от покупки такого удилища. В некоторых случаях склонность к переколебаниям сознательно заложена в строй, однако чаще она является паразитным свойством удилища — когда недостаточный модуль используемого материала не позволяет ее избежать.
Считается, что «стекло» (и удилища из низкомодульных материалов вообще) лучше себя проявляет с теми типами приманок, которые предназначены для равномерной проводки. «Стеклянный» спиннинг не рвет рыбе губу и обладает определенными преимуществами при вываживании. Даже и среди «стекла» наблюдается широкий разброс по модулю упругости — от 6 млн. (E-glass) до 13 млн. (S-glass). Однако для наших с вами задач нужен модуль от 30 млн. единиц и выше, который недостижим для «стекла», но является вполне обычным для углепластика.
В прежние времена чувствительным называли удилище, которое главным образом по зрительному восприятию передавало максимум информации о происходящем с приманкой — ее ход, игру и, разумеется, поклевку. Зрительное восприятие касалось прежде всего самого кончика спиннинга — именно он служил основным индикатором проводки и поклевки. Непосредственно в руку, держащую удилище, что-то если и передавалось, то в очень и очень ослабленном виде….
Собственно, и сейчас кончик спиннинга остается для нас одним из источников информации, но роль его уже отнюдь не исключительна. С появлением и совершенствованием «углевых» удилищ все большее значение стало приобретать не визуальное, а мышечное восприятие проводки и поклевки рыбы.
По-настоящему чувствительный спиннинг дает возможность без напряжения, не глядя на вершинку и на леску, отчетливо ощущать все происходящее с приманкой. Это качество очень важно отнюдь не только для ловли, например, в темное время или для людей с неидеальным зрением. Чувствительность «в руку» делает процесс ловли более комфортным и менее утомительным, особенно когда речь идет о ловле на джиг. Кроме того, восприятие через мышечные рецепторы значительно сокращает интервал времени между поклевкой и подсечкой. И это уже не только практический рыболовный опыт, но и данные нейрофизиологической науки. Рука реагирует быстрее на то, что она непосредственно ощущает, нежели когда в роли приемника информации выступает глаз…
Насколько все это серьезно — попробуйте решить для себя сами. Все-таки спиннинги с чувствительностью «на глаз» были, есть и будут. Тем более что основная их масса принадлежит к недорогому, или народному, классу. Если же вы склоняетесь к выбору удилища с чувствительностью «в руку», то здесь надо иметь в виду несколько принципиальных моментов.
Первое. При прочих равных условиях более чувствительным будет тот спиннинг, бланк которого изготовлен из более модульного материала. Под модулем изначально подразумевается известный из школьного курса физики модуль упругости Юнга.
Наверное, нет особой необходимости лишний раз пояснять, что это такое — кто знает, тот в том не нуждается, кто не знает, тому оно вроде как и не интересно. Однако здесь стоит сделать одно существенное замечание. Разные фирмы, поставляющие на рынок спиннинговые удилища, пользуются разными системами количественной оценки модульных характеристик своих удилищ. Иными словами, впрямую сравнивать по заявленной модульности можно только удилища от одной фирмы.
Что еще важно — модуль упругости это внутренняя характеристика исходного материала бланка. То, что получается на выходе (то есть готовые удилища) при одинаковом исходном модуле могут иметь существенно разную чувствительность, поскольку она зависит и от других факторов.
Второе. С увеличением модуля графита возрастает его цена и обостряется вопрос «выживаемости»: спиннинг из высокомодульного «угля» требует к себе более аккуратного обращения. Попытки создать одновременно дешевое и «звонкое» (то есть чувствительное за счет модульности) удилище, как правило, не очень удачны. В последнее время на рынке появилось изрядное количество китайских удилищ этого рода, которые, вроде бы, производят приятное начальное впечатление, но вот статистика поломок по ним в итоге оказывается просто неприличной.
Некоторые вопросы конструкций удилищ
Выбор подходящего спиннинга это проблема, решаемая по разному: в лоб по принципу — чем дороже, тем лучше, по степени доверия к фирме, по чьему-то совету или по собственной интуиции. Цена вопроса в денежном эквиваленте довольно высока, а информации крайне мало. Ассортимент в магазинах огромен и при этом отсутствует единая классификация. Единственный параметр, предлагаемый покупателю это массовый тест, но не все хорошо представляют себе, что это такое. Основные параметры конструкционных материалов хлыста нигде не сертифицируются. Каждая фирма — изготовитель естественно предлагает самое-самое. Специалисты говорят разное: одни, что должен быть параболический строй другие, что бывают удочки быстрые или не очень, а один сказал, растопырив пальцы, что это должно быть черным и тока от Гарри Лумиса, ну типа как у меня. Конечно, серьезные фирмы считают свои хлысты, но информацией не делятся, видимо имея на то причины, которых позже слегка коснемся.
Кроме эстетического услаждения своего владельца (что тоже конечно крайне важно) у любого удилища есть две функциональные обязанности — это заброс приманки и вываживание добычи. Последняя самая радостная стадия, как и большинство систем с биологическими объектами практически не поддается расчетам из-за многовариантности поведения последних. Описывая процесс качественно можно сказать, что ввиду наличия даже малого момента инерции у шпуль катушек всех типов растягивающее усилие на леске при резком рывке может значительно превышать установленное на тормозном фрикционе. Амортизацию таких рывков производит упругая конструкция хлыста, а вот доверять ситуацию полностью тормозам катушки можно только имея двух — трех кратный запас разрывной прочности.
Для производства современных спиннингов и нахлыстовых удилищ применяются композиционные материалы. Упрочнителями служат волокна: стеклянные, углеродные, борные и их разнообразные сочетания, уложенные слоями под разными углами. Содержание их в материале достигает 60 — 80 об %. Прочность и модуль упругости композита определяется свойствами упрочнителя. Матрица только связывает композицию, придавая ей форму. Как правило, это полимер: чаще всего встречаются эпоксидная фенолоформальдегидная или полиамидная матрица.
Ранее других появился ориентированный стеклопластик. Его недостаток это невысокий модуль упругости: Е ~ 60 Гпа, 0,6*105 h/mm2. Материал обладает высокой выносливостью на изгиб до 2*107 циклов, хорошим относительным удлинением при разрыве ~ 2 % технологичен и дешев. Его применение, на мой взгляд, полностью оправдано для удилищ с массовым тестом > 50 гр.
Карбоволокниты (углепласты) содержат углеродные волокна иногда с примесью стекловолокон. Модуль упругости на растяжение Е=150 — 200 Гпа, 1,5-2,0*105 h/mm2. Относительное удлинение при разрыве около 0,5 %. Обладают высокой электропроводностью. Устойчивы к воздействию агрессивных сред и излучения. Высокое статическое и динамическое сопротивление усталости сохраняется при нормальной и очень низкой температуре (высокая теплопроводность предотвращает саморазогрев за счёт внутреннего трения). Недостаток — технологически сложный процесс изготовления и соответственно высокая себестоимость.
Бороволокниты (упрочнитель — борные волокна) отличаются высокой прочностью Е > 200 Гпа, 2,0*105 h/mm2 и твердостью. Ячеистая микроструктура борных волокон обеспечивает высокую прочность при сдвиге на границе раздела с матрицей. Относительное удлинение на разрыв около 0,4%. Полупроводник. Для облегчения технологического процесса применяются комплексные боростеклониты, в которых несколько параллельных борных волокон оплетаются стеклонитью придающей формоустойчивость.
В заключение интересно привести значения модуля продольной упругости для некоторых материалов:
Сталь 195 / 210 Гпа 1,95 / 2,1*105 h/mm2
Алюминий 70 Гпа 0,7*105 h/mm2
Дерево 10 / 12 Гпа 0.1/0.12*105 h/mm2.
Таким образом, видно, что композиты по удельной жесткости (жесткость на единицу массы) в несколько раз превосходят обычные материалы. На практике это показатель, определяющий вес удочки с заданной жесткостью, которая достигается необходимой толщиной стенок полого трубчатого хлыста. Сравнивая между собой композиты, надо отметить, что углепласт на четверть легче бороволокнита, а это полностью компенсирует его меньший модуль упругости. Другой путь повышения жесткости конструкции не приводящий к увеличению веса лежит в увеличении наружного диаметра самой трубки. Следует отметить снижение величины относительного удлинения при разрыве с увеличением модуля упругости (удельная прочность однонаправленного стекловолокна в несколько раз выше бороволокна), что означает уменьшение допустимого угла изгиба удилища и накладывает ограничения на предельный внешний диаметр. Проще говоря, высокомодульный углепласт сломать намного проще дешевой удочки из стекловолокна, низкий модуль упругости которого можно компенсировать увеличением геометрии конструкции. В отношении бамбуковых удилищ вопрос сложнее, но преимущество синтетики это технологичность и инертность ко всякого рода воздействиям.
Изгибаясь самым невероятным образом, спиннинг работает в предельных режимах многократной деформации. Современные композиционные материалы допускают несколько миллионов подобных циклов и тысячи часов длительного изгиба. К сожалению подобного нельзя сказать о декоративных покрытиях, которые к тому же ухудшают упругие свойства или попросту скрывают дефекты самого бланка. По условиям эксплуатации на рыбалке композиты не нуждаются в защите. От механических повреждений хорошо предохраняет тубус и бережное отношение. Самая прочная конструкция с точки зрения теории должна иметь ровную полированную естественную поверхность.
Модуль: чем больше, тем лучше.
Прежде, чем рассматривать, как величина модуля волокон влияет на свойства спиннинга необходимо понять, что же собственно представляет собой этот модуль?
Определение из учебника по сопротивлению материалов: Коэффициент пропорциональности Е, связывающий нормальное напряжение и относительное удлинение, называется модулем упругости.
Другими словами, чем больше модуль, жестче стержень при тех же размерах.
В международной системе единиц модуль Е измеряют в тех же единицах, что и механическое напряжение или давление, т.е. в Па (паскаль). Поскольку численные значения модуля весьма большие, для компактности записи применяют приставку Г(гига), означающую миллиард. Пример модулей упругости материалов: стекловолокно 95-100 ГПа, сталь 195-205 ГПа, углеродное волокно 216-677 ГПа, вольфрамовая проволока 420 ГПа.
Модуль упругости материала численно равен механическому напряжению, которое необходимо создать в стержне, чтобы растянуть его в два раза.
А как влияет величина модуля волокон на свойства спиннинга?
Если критерием качества спиннинга считать модульность исходного материала, то спиннинги, изготовленные из стали и низкомодульного углеродного волокна будут обладать одинаковыми свойствами. Очевидно, что это не так.
Критерием качества материала для спиннинга является не величина модуля упругости и прочность, а отношение этих величин к массе, т.е. удельная прочность и удельная жесткость. По указанным параметрам углеродные волокна превосходят лучшие стали и титановые сплавы в несколько раз.
Чтобы наглядно представить, как влияет модуль на свойства бланка, проведем мысленный эксперимент.
Представим себе некоторый бланк, изготовленный из материала модулем, равным скажем Е некоторых единиц. Предположим, что мы приложили к нему максимально допустимую нагрузку, и он получил некую деформацию. Если модуль материала спиннинга увеличить в два раза, то под воздействием той же нагрузки он деформируется в два раза меньше, а накопленная потенциальная энергия уменьшится в четыре раза. Если попытаться деформировать спиннинг до прежней величины, то он сломается. В конечном результате мы получим спиннинг с более узким тестовым диапазоном, поскольку верхняя граница теста не изменится, а нижняя сильно возрастет.
Если одновременно с модулем увеличить вдвое прочность материала, то увеличится верхняя граница теста, и мы получим более совершенный спиннинг, но в другом весовом классе.
Чтобы вернутся к исходному весовому классу, мы можем уменьшить диаметр бланка или толщину стенок. При тех же упругих и прочностных свойствах мы получим боле легкий и, следовательно, более быстрый бланк.
Отсюда вывод: увеличение модуля упругости материала бланка оправдано только при одновременном увеличении прочности.
Структура углеродного волокна зависит от исходного сырья, состава макромолекул, степени вытяжки волокон, технологии их получения и многих других параметров. В связи с этим углеродные волокна, получаемые из разных синтетических волокон, имеют разное соотношение модуля упругости и прочности. Величина модуля упругости никак не связана с прочностью волокна.
Но даже лучшее углеродное волокно – это просто пучок ломких нитей. Чтобы получить из отдельных нитей высокопрочный материал, их необходимо соединить в одно целое посредством связующего вещества. Свойства конечного материала будут очень сильно зависеть от технологии укладки, уплотнения степени ориентированности и еще многих других параметров, определяемых технологией изготовления. Причем модуль упругости получаемого углепластика практически не изменится, а вот прочность, особенно удельная, целиком определяется технологией изготовления бланка.
Очень важно понимать тот факт, что жесткость удилища определяется не только модулем упругости материала, но и наружным диаметром, толщиной стенок и длиной.
Т.е. жесткость удилища определяется как модулем материала, так и геометрией бланка.
Важнейшее прочностное свойство углепластика – ударная вязкость, т.е. способность противостоять ударам целиком определяется технологией изготовления бланка и никак не зависит от изначальных свойств волокон
Углеволокно имеет определённые показатели прочности и способности сопротивляться растяжению. От способов производства углеволокна зависят эти характеристики. Но бланк — это композиционный материал, состоящий из углеволокна и связующего. Вторая часть не менее важна, чем первая, равно и характер их взаимодействия (адгезия и прочая). Но об этой второй части производители молчат в большинстве случаев. Ну представьте: вы строите 9-этажный дом из монолитного бетона. И будете покупателям квартир рассказывать, что у вас стоит титаново-углеволоконная арматура, аналогов которой нет. А бетончиком-то её завливаете марки М50, который пальцем ткни — рассыплется. Так и со всеми этими IM6-IM10.
Выводы:
1. Жесткость бланка, модуль упругости материала бланка и модуль упругости исходных углеродных волокон – это совершено разные характеристики.
2. Высокий модуль материала без высокой прочности бесполезен.
3. Увеличение модуля упругости материала бланка имеет смысл при одновременном увеличении прочности.
4. Высокая удельная прочность важнее, чем высокий модуль.
5. Величина модуля и прочность материала никак не связаны между собой.
6. Величину удельной прочности производители указывают.
7. Свойства бланка гораздо больше зависят от технологии изготовления и конструкции, чем от изначальных свойств углеволокна.
8. Для спиннингистов – практиков знание этих параметров не обязательно, и даже вредно, поскольку затуманивает объективное восприятие качества бланка.
Окончательный вывод: величина изначального модуля упругости углеродных волокон, без указания других параметров не дает никакой информации о свойствах бланка.
И, наконец, информация для размышления: материалы, из которых изготовлены консервная банка и лезвие хорошего ножа, имеют одинаковый модуль упругости
https://menstois.ru
Применение углеволокна (карбона) в строительстве
Беседка из углепластикаНа сегодняшний день с изделиями из бетона и стали успешно соперничают материалы из шнуров, тканей, волокон и лент изготовленных из современных углеводородов. При этом такие материалы обладают небольшой толщиной и весом.
Даже холст толщиной всего в несколько миллиметров, пропитанный отвердевшей смолой по своей прочности превосходит 15 миллиметровый лист фанеры и в пять раз прочнее стали.
Содержание статьи
Что такое углеродные волокна
Улеволокно (карбон) представляет собой полимерно-композитный материал, в основе которого лежат углеродные нити. Имеет наибольшую популярность среди других пластиков и композитов. Имея четырёх кратную прочность на разрыв, чем у наилучших марок стали, углеволокно намного легче железа (на 75%) и алюминия (на 30%).
Углеродные нити достаточно ломкие и поэтому из них создают эластичное полотно. А добавление полимерных связующих составов позволяет изготавливать углепластик, совершивший революцию во множестве сфер деятельности человека.
Для чего нужен карбон (углеволокно)
Углеродные волокна представляют собой альтернативу традиционным материалам, например, стали, алюминию, стеклопластику и для строительства легких ферм и каркасных конструкций. Они обладают высокой прочностью, надежностью, возможностью настройки, и имеют малый вес.
Углеволокно на данный момент пользуется большим спросом у строителей и ремонтников. Подобная популярность обусловлена высокой прочностью материала. Это качество очень важно при обустройстве внешнего армирования кирпичных, железобетонных и деревянных систем.
Конструкция, оклеенная углеволокном, получает дополнительно до 60 % прочности и до 110 % прочности на сжатие. Хоть и выглядит это не достаточно правдоподобно, все проверки по СНиП и ГОСТ это подтверждают. Поэтому, если собираетесь делать ремонт или занимаетесь строительством, можете в серьез подумать об усилении из карбона.
Усиление прочности конструкции позволяет сократить размеры основания. Углеволокно удерживает на себе значительные нагрузки, самое главное, чтобы было, куда его приклеить. Сокращение необходимого материала за счет использования современного карбона является актуальным мероприятием для отдаленных регионов, куда сложно доставить тяжелые строительные материалы.
Помимо этого углеволокно сейчас используют при ремонте несущих элементов из камня. Путем армирования восстанавливаются балки и опоры бетонных мостов. Как правило, используется карбон в промышленности, но может применяться и в частном строительстве, где нагрузки значительно ниже, а значит, запас прочности будет довольно большим.
Достоинства материала
Многие знают о коррозии сборного железобетона, которую вызывает стальная арматура. При использовании сетки из углеродного волокна вместо стальной арматуры результаты получаются превосходными.
- Бетонные стеновые панели можно делать намного тоньше.
- Вес панелей становиться намного легче (до 75%).
- Не требуется дополнительная теплоизоляция потому, что углеволокно не проводит тепло или холод.
- Обладает высокой огнестойкостью.
- Этот новый материал уже используется для производства стеновых сендвич панелей.
Недостатки
Углеродное волокно также имеет недостатки, которые должны быть приняты во внимание при планировании его использования.
- Этот материал довольно дорогой по сравнению с аналогами.
- Материал имеет способность отражать электрические волны, что может быть недостатком в некоторых случаях.
- Процесс изготовления композитов более трудоемкий, чем изготовление металла.
Что такое углеродное волокно? | DragonPlate
Углеродное волокно состоит из атомов углерода, связанных вместе в длинную цепочку. Волокна чрезвычайно жесткие, прочные и легкие и используются во многих процессах для создания превосходных строительных материалов. Углеродный волокнистый материал входит в состав множества «сырых» строительных блоков, включая пряжу, однонаправленную пряжу, переплетения, тесьму и некоторые другие, которые, в свою очередь, используются для создания композитных деталей из углеродного волокна.
Внутри каждой из этих категорий есть множество подкатегорий, требующих дальнейшего уточнения.Например, различные типы переплетения углеродного волокна приводят к различным свойствам композитной детали как при производстве, так и в конечном продукте. Чтобы создать композитную деталь, углеродные волокна, которые жесткие при растяжении и сжатии, нуждаются в стабильной матрице, чтобы оставаться в ней и сохранять свою форму. Эпоксидная смола — это превосходный пластик с хорошими характеристиками сжатия и сдвига, который часто используется для образования этой матрицы, при этом углеродные волокна обеспечивают армирование. Поскольку эпоксидная смола имеет низкую плотность, можно создать легкую, но очень прочную деталь.При изготовлении композитной детали можно использовать множество различных процессов, включая мокрую укладку, вакуумную упаковку, перенос смолы, согласованные инструменты, формование со вставкой, пултрузию и многие другие методы. Кроме того, выбор смолы позволяет адаптировать ее к конкретным свойствам.
Углеродные волокна, армирующие стабильную эпоксидную матрицу
Прочность, жесткость и сравнение с другими материалами
Углеродное волокно чрезвычайно прочно. В инженерии типично измерять преимущество материала с точки зрения отношения прочности к весу и отношения жесткости к весу, особенно при проектировании конструкций, где добавленный вес может привести к увеличению затрат на жизненный цикл или неудовлетворительным характеристикам.Жесткость материала измеряется его модулем упругости. Модуль упругости углеродного волокна обычно составляет 33 мси (228 ГПа), а его предел прочности на разрыв обычно составляет 500 фунтов на квадратный дюйм (3,5 ГПа). Материалы из углеродного волокна с высокой жесткостью и прочностью также доступны благодаря специальным процессам термообработки с гораздо более высокими значениями. Сравните это с 2024-T3 Aluminium, который имеет модуль упругости всего 10 msi и предел прочности на разрыв 65 ksi, и 4130 Steel, который имеет модуль упругости 30 msi и предел прочности на растяжение 125 ksi.
Сталь будет постоянно деформироваться при уровне напряжения ниже ее предела прочности на разрыв. Уровень напряжения, при котором это происходит, называется пределом текучести. Углеродное волокно, с другой стороны, не будет постоянно деформироваться ниже своего предела прочности на разрыв, поэтому оно фактически не имеет предела текучести.
В качестве примера, ламинат, армированный углеродным волокном с полотняным переплетением, имеет модуль упругости приблизительно 6 м / кв. Дюйм и объемную плотность приблизительно 83 фунта / фут 3 . Таким образом, весовая жесткость этого материала составляет 107 футов.Для сравнения, плотность алюминия составляет 169 фунтов / фут 3 , что дает жесткость к весу 8,5 x 106 футов, а плотность стали 4130 составляет 489 фунтов / фут 3 , что дает жесткость к весу 8,8 x 106 футов. Следовательно, даже основная панель из углеродного волокна с полотняным переплетением имеет отношение жесткости к весу на 18% больше, чем у алюминия, и на 14% больше, чем у стали. Использование препрега, в частности высокомодульных и сверхвысокомодульных препрегов из углеродного волокна, дает существенно более высокое соотношение жесткости к массе.Например, панель, содержащая слой стандартного углеродного волокна препрега со стандартным модулем упругости 0/90, будет иметь модуль изгиба примерно 8 мсек, или примерно на 30% жестче, чем варианты без препрега. Для очень требовательных применений, где требуется максимальная жесткость, можно использовать сверхвысокомодульное углеродное волокно 110 м / кв. Это специализированное углеродное волокно на основе пека имеет жесткость на изгиб в 3 раза больше, чем у стандартной панели из препрега с модулем упругости (около 25 мсек). Если учесть возможность индивидуальной жесткости панели из углеродного волокна за счет стратегического размещения ламината, панель (или другое поперечное сечение, например труба) может быть изготовлена с жесткостью на изгиб порядка 50 мси.
Испытания, проведенные Dragonplate, показали, что все образцы однонаправленных сверхвысокомодульных образцов с нулевой ориентацией имеют жесткость на растяжение, превышающую 75 мсю, или более чем в два раза жесткость стали, но все же только половину веса алюминия. Если использовать вышеупомянутое сравнение, то отношение жесткости к весу этого материала более чем в 10 раз больше, чем у стали или алюминия. Если учесть потенциально значительное увеличение как прочности к весу, так и отношения жесткости к весу, которое возможно, когда эти материалы сочетаются с легкими сотами и вспененными сердцевинами, очевидно ли, какое влияние усовершенствованные композиты из углеродного волокна могут оказать на широкий спектр применений.
Что такое композитная многослойная структура?
Композитный сэндвич сочетает в себе превосходные характеристики прочности и жесткости углеродного волокна с материалом сердцевины меньшей плотности. В случае сэндвич-листов Dragonplate углеродное волокно создает тонкую ламинатную пленку над сердцевиной из пенопласта, соты, бальзы или березовой фанеры. Стратегически комбинируя эти материалы, можно создать конечный продукт с гораздо более высоким соотношением жесткости к весу, чем с любым из них по отдельности. Для приложений, где вес имеет решающее значение, сэндвич-листы из углеродного волокна могут быть подходящими.
Композитная многослойная конструкция механически эквивалентна однородной двутавровой конструкции при изгибе.
Рис. 1: Схема, показывающая многослойную конструкцию из углеродного волокна и эквивалентную двутавровую балку
На изображении многослойной конструкции в центре балки (при допущении симметрии) находится нейтральная ось, где находится внутреннее осевое напряжение равно нулю. Двигаясь снизу вверх на диаграмме, внутренние напряжения переключаются с сжатия на растяжение.Жесткость на изгиб пропорциональна моменту инерции поперечного сечения, а также модулю упругости материала. Таким образом, для максимальной жесткости на изгиб следует размещать чрезвычайно жесткий материал как можно дальше от нейтральной оси. Путем размещения углеродного волокна как можно дальше от нейтральной оси и заполнения оставшегося объема материалом с более низкой плотностью в результате получается композитный многослойный материал с высоким отношением жесткости к весу.
Рисунок 2: Сравнение распределения внутренних напряжений для сплошного ламината и многослойной конструкции при изгибе.
Анализ FEA для сравнения многослойного ламината с твердым углеродным волокном показан ниже. Эти расчеты показывают прогиб консольной балки с нагрузкой на конец. На рисунке показан слой сердцевины из березовой фанеры толщиной 3/16 дюйма рядом со слоем твердого углеродного волокна равного веса. Из-за уменьшенной толщины твердой углеродной балки он отклоняется значительно больше, чем эквивалентная балка, изготовленная из материала сердцевины. По мере увеличения толщины это несоответствие становится еще больше из-за значительной экономии веса сердечника.Аналогичным образом, можно заменить твердую углеродную структуру на более легкую, эквивалентную прочности и жесткости, сделанную из любого из ранее упомянутых вариантов сердечника.
Рис. 3: Сравнение анализа методом конечных элементов между многослойным слоистым материалом Dragonplate и твердым углеродным волокном
При использовании различных сердцевин каждый имеет свои сильные и слабые стороны. Обычно движущими факторами являются прочность сердечника на сжатие и сдвиг. Например, если требуется высокая прочность на сжатие (и, следовательно, высокое сопротивление раздавливанию), то сердцевина, скорее всего, должна быть более высокой плотности (здесь хорошими вариантами являются пенопласт высокой плотности или березовая фанера).Если, однако, нужен композит с абсолютно наименьшим возможным весом, а напряжения относительно малы (т. Е. Низкая нагрузка, высокая жесткость), то лучшим выбором может быть чрезвычайно легкий пенопласт или сотовый заполнитель. Некоторые сердечники обладают лучшей влагостойкостью (пенопласт с закрытыми порами), некоторые — лучшей обрабатываемостью (фанера), а другие — высоким отношением прочности на сжатие к весу (бальза). Задача инженера — понять компромиссы в процессе проектирования, чтобы максимально использовать потенциал композитных материалов с сердечником.Тем не менее, для критичных по весу приложений часто нет другого варианта, который даже приблизился бы к потенциальной прочности и соотношению жесткости к весу ламинатов с многослойным сердечником из углеродного волокна.
КРИТЕРИИ СРАВНЕНИЯ | |||||
ПРОДУКТЫ | Жесткость к массе | Прочность | Измельчение | Устойчивость к влаге | Звукоизоляция | Углеродное волокно Твердое
ЛУЧШЕ | ЛУЧШЕ | СЛАБЫЕ | |||
Твердое углеродное волокно с высоким модулем упругости | ЛУЧШЕ | ХОРОШО | ЛУЧШЕ | ЛУЧШЕ | СЛОЖНО |
Березовое ядро | ЛУЧШЕ | ЛУЧШЕ | ХОРОШО | ПЛОХО | |
Бальзовое ядро | ЛУЧШЕ | ХОРОШО | ЛУЧШЕ | ПЛОХО | ХОРОШО |
Nomex Honeycomb Core | НАИЛУЧШЕ | ХОРОШО | ЛУЧШЕ | ||
Depron Foam Core | ЛУЧШЕ | ПЛОХО | ПЛОХО | ЛУЧШЕ | ЛУЧШЕ |
Airex Foam Core | BEST | ХОРОШО | ХОРОШО | ЛУЧШЕ | ЛУЧШЕ |
Divine Core | ЛУЧШЕЛУЧШЕ | ЛУЧШЕ | ЛУЧШЕ | ХОРОШО | |
Last-A-Foam Core | ЛУЧШЕ | ЛУЧШЕ | ЛУЧШЕ | ЛУЧШЕ | ЛУЧШЕ |
Карбоновое волокно
Плюсы и минусы Армированные композиты обладают несколькими очень желательными характеристиками, которые можно использовать при разработке современных материалов и систем.Два наиболее распространенных применения углеродного волокна — это приложения, где высокая прочность по отношению к весу и высокая жесткость по отношению к весу составляют
Прочность углеродных волокон — Big Chemical Encyclopedia
Для материалов носовой части формируются угольные заготовки, армированные в трех направлениях (3D), с использованием ячеек небольшого размера для равномерного удаления и малых размеров пор. На рис. 5 показаны типичные размеры элементарной ячейки для двух наиболее распространенных материалов трехмерной носовой части. Плетеные углеродно-углеродные преформы изготавливаются с различными размерами ячеек для различных применений (27–33).Волокна, общие для этих композитов, включают в себя вискозное волокно, полиакрилонитрил и углеродные волокна-предшественники пека. Прочность этих волокон составляет от 1 до 5 ГПа (145 000–725 000 фунтов на кв. Дюйм), а модуль упругости — от 300 до 800 ГПа. [Pg.5] Рис. 6. Каждая температура карбонизации зависит от прочности и модуля упругости углеродного волокна на основе ПАН (31). Чтобы преобразовать ГПа в фунты на квадратный дюйм, умножьте его на 145000.
Юнг, Т., Субраманиан Р. и Маноранджан В. (1993). Прогнозирование прочности волокна на критической длине. Теория моделирования и экспериментальная проверка бимодально распределенной прочности углеродного волокна. J. Mater. Sci. 28, 4489-4496. [Pg.88] В таблице I показаны механические свойства ПТФЭ, армированного углеродным волокном (несшитый композит ПТФЭ) и ПТФЭ, армированного углеродным волокном, с фторированным пеком (композит ПТФЭ / ФП, термохимически сшитый). Для испытания на растяжение с направлением 45 ° плоской тканой углеродной ткани предел прочности композита ПТФЭ / ФП составлял около 2.В 3 раза выше, чем у несшитого композита ПТФЭ. Более того, модуль Юнга сшитого композита был примерно в 2,6 раза выше, чем у композита ПТФЭ. Прочность на разрыв и модуль Юнга являются результатом направления 0 ° или 90 ° для ткани, отражающего прочность и модуль углеродного волокна.
Рис. 3.21. Влияние различных типов дефектов на распределение прочности углеродного волокна (a) Исходные дефекты поверхности…
В производственном процессе автор отдает предпочтение этому методу. Такаку и др. [90] стабилизировали предшественник AN / MA при 240, 255 и 270 ° C и наблюдали увеличение окисленной плотности, которая достигла постоянного значения 1,58 г · см при более длительном времени стабилизации, получая оптимальную прочность углеродного волокна с окисленным плотность около 1,375 г см (рис. 5.37). Баджадж и Рупанвал [91] объяснили увеличение плотности более плотной упаковкой молекулярных цепей из-за циклизации нитрильных групп.[Pg.216] В одной из печей окисления произошел выброс экзотермических газов, и произошел выброс выделяющихся газов, которые сместили защитное покрытие взрыва, расположенное в верхней части печи. Такой случайной перестановки одеяла замечено не было. Однако это совпало с увеличением прочности углеродного волокна. Впоследствии было установлено новое постоянное положение для одеяла, чтобы воспользоваться этим преимуществом в прочности углеродного волокна. [Pg.422]
Дымовой карандаш следует использовать для проверки на проникновение воздуха.Печь можно правильно сбалансировать, отрегулировав основной поток N2 на входном конце печи до такого уровня, чтобы при взгляде вниз в муфель печи атмосфера не была полностью прозрачной, но в то же время дым не вытеснялся. от выходного конца. Очень важно поддерживать легкую мутную атмосферу, так как это позволяет нужной концентрации HCN накапливаться в печи, значительно улучшая прочность углеродного волокна. [Pg.441]
Таблица 18.1 Случайная выборка из 100 углеродных волокон (ГПа), расположенных в порядке возрастания …
Рейнольдс, W.N. и Sharp, J.V. (1974) Предел прочности углеродного волокна на сдвиг кристалла. Углерод, 12103-110. [Pg.179] До сих пор важность химии углеродных кластеров заключалась в открытии новых знаний. Многие ученые считают, что самые ранние промышленные применения фуллеренов будут основаны на их новых электрических свойствах. Бакминстерфуллерен является изолятором, но имеет высокую сродство к электрону и является сверхпроводником в его восстановленной форме. Нанотрубки вызвали большой интерес из-за их электрических свойств и в качестве потенциальных источников углеродных волокон большой прочности… [Pg.437]
Другими армирующими элементами, которые могут использоваться в слоях подложки декоративных ламинатов и в структуре промышленных ламинатов, являются тканые ткани из стекла или холста и нетканые материалы из различных полимерных моноволокон, таких как полиэстер, нейлон или углеродные волокна. Тканые и нетканые материалы, как правило, намного прочнее бумаги и имеют гораздо более однородную прочность по всей плоскости x-y. Они значительно улучшают такие свойства ламината, как ударопрочность и прочность на разрыв.[Pg.532]
Углеродно-волоконные композиты. Отвержденные ламинаты из фенолегиднокислых смол и армирования углеродным волокном обеспечивают превосходную огнестойкость и термостойкость по сравнению с ненасыщенными полиэфиром и эпоксидной смолой. В таблице 15 показана зависимость прочности на изгиб и модуля упругости для композитов фенонНс — углеродное волокно при содержании 30-40% смолы феногс (91). Эти композиты также обладают длительной стабильностью при повышенных температурах до 230 ° C. [Стр.307]
Таблица 15. Прочностные свойства фенольных композитов с углеродным волокном…
Углерод, карбиды и нитриды. Углерод (графит) является хорошим проводником тепла и электричества. Он плохо смачивается химическим воздействием, что является важным фактором коррозионной стойкости. Как важный структурный материал при высоких температурах, пиролитический графит показал прочность 280 МПа (40 600 фунтов на кв. Дюйм). Он склонен к окислению при высоких температурах, но его можно использовать при температуре до 2760 ° C в течение короткого времени в нейтральных или восстановительных условиях.Ожидается использование новых композитных материалов из углеродных волокон, особенно в области аэрокосмической конструкции. При нагревании под … [Pg.26] Рис. 1. Удельная прочность и модуль Юнга различных конструкционных материалов, где CF = углеродное волокно, HM / UHM = высокий модуль / сверхвысокий модуль …
Углеродные волокна обычно подразделяются на предшественники, такие как ПАН, пек или искусственный шелк, и классифицируются по модулю упругости и прочности.Классы модуля упругости при растяжении варьируются от низкого (физические свойства имеющихся в продаже углеродных волокон представлены в таблице 1. [Pg.2] Исходное волокно затем промывается и растягивается до низкого текс (денье), необходимого для обработки углеродного волокна. значительная ориентация молекул полимера и обеспечивает основу для структуры высокоориентированного углерода, которая образуется после карбонизации.Особое внимание уделяется тому, чтобы избежать загрязнения или примесей, которые могут образовывать дефекты, снижающие прочность углеродного волокна.[Pg.3]
Алюминий и углеродное волокно — сравнение материалов
Какой материал может заменить алюминий и обеспечить повышенную прочность, а также меньший вес?
Можно ли производить компоненты, которые весят на 50% меньше алюминия, но обладают такой же или большей прочностью?
Алюминий — широко используемый материал, но углеродное волокно представляет собой новое решение для многих инженеров-строителей. В этой статье указаны различия между этими материалами и описаны их сильные и слабые стороны.
Каковы сильные и слабые стороны этих материалов?
Прочтите эту статью, чтобы узнать больше о сильных и слабых сторонах алюминия и углеродного волокна.
Введение
Углеродное волокно используется в отраслях, где требуется высокая прочность и жесткость по отношению к весу. например в авиации, автоматизированные машины, гоночные автомобили, профессиональные велосипеды, реабилитационное оборудование.
Благодаря своему уникальному дизайну углеродное волокно также используется в производстве предметов роскоши, включая часы, кошельки и т. Д.Этот материал делает продукт уникальным в мире роскоши и элегантности и помогает ему быть на шаг впереди конкурентов.
Сопоставить свойства углеродного волокна со сталью или алюминием непросто. В отличие от углеродного волокна, металлы обычно однородны. — изотропны, что обеспечивает одинаковые свойства во всех направлениях.
Прочность и жесткость компонента из углеродного волокна достигается путем размещения тканей определенным образом. Это открывает возможности для производителя, но также требует больших знаний и опыта.
В этом исследовании анализируются 10 наиболее важных свойств для инженеров-строителей:
- Жесткость и прочность материала по отношению к весу.
- Жесткость и прочность материала одинаковой толщины.
- Вес / плотность.
- Механическая обработка.
- Тепловое расширение.
- Теплопроводность.
- Температурная стойкость
- Долгосрочная работа.
- Осуществление производственного процесса.
- Сводка
Обратите внимание, что любое упоминание углеродного волокна и его характеристик в этом документе относится к композитному материалу, изготовленному из углеродного волокна и эпоксидной смолы.
1. Жесткость и прочность материала по отношению к весу
Чтобы объяснить жесткость в зависимости от веса, представьте себе лист шириной 5 см, длиной 50 см и толщиной 2 мм. Когда вы подвешиваете груз весом 5 кг к концу листа, нагрузка приведет к изгибу, а степень изгиба будет соответствовать жесткости.Для разных материалов лист одинаковой толщины будет иметь разные свойства изгиба. Чем жестче материал, тем меньше будет изгибов. После снятия нагрузки лист примет первоначальную форму.
А теперь представьте, что полоса материала подвергается более высокой нагрузке — это вызовет податливость полосы и после снятия нагрузки полоса восстанавливает свою первоначальную форму. Это сила делает это возможным. Чем выше прочность материала, тем большую нагрузку ему потребуется, прежде чем последует постоянная текучесть.
Помимо прочности и жесткости, еще одним важным свойством для инженеров-проектировщиков является вес элемента, который определяется плотностью.
Жесткость материала измеряется модулем Юнга. Однако одного этого параметра недостаточно для определения жесткости материала без учета веса данного элемента.
Например, в случае рамы велосипеда (размеры, геометрия, толщина стенки), изготовленной из двух разных металлов: стали и алюминия, стальная будет иметь в 3 раза большую жесткость, чем алюминиевая. Но если еще учесть вес элементов, то стальная рама, хотя она имеет в 3 раза большую жесткость, чем алюминиевая, она также будет в 3 раза тяжелее .
Эти числа являются приблизительными, поскольку на практике инженер-конструктор указывает геометрию для выбранного материала, например в случае алюминиевой рамы велосипеда чаще всего увеличивают диаметр рамы и толщину стенок. В случае велосипедной рамы жесткость и прочность напрямую связаны с геометрией и толщиной стенок (увеличение толщины стенки в 2 раза приводит к увеличению жесткости примерно в 8 раз).
Прочность зависит не только от материала и толщины секции, но и от ее геометрии.На самом деле существует много разных факторов, но именно отношение жесткости материала к его весу является общим знаменателем и упрощает сравнение и анализ различных материалов.
Отношение жесткости к весу (а именно удельный модуль) на практике является наиболее эффективным для определения жесткости материала , поскольку для большинства инженеров-конструкторов жесткость и вес являются наиболее важными параметрами.
Углеродное волокно — это материал, обладающий жесткостью и прочностью при низкой плотности. — он легче алюминия и стали, что дает много практических преимуществ.
Вес к весу, углеродное волокно предлагает от 2 до 5 раз большую жесткость (в зависимости от используемого волокна) , чем алюминий и сталь . В случае отдельных компонентов, которые будут подвергаться нагрузке только в одной плоскости, изготовленных из однонаправленного углеродного волокна, его жесткость будет в 5-10 раз больше, чем у стали или алюминия (того же веса).
В следующих таблицах сравниваются жесткость и устойчивость к повреждениям для различных материалов одинакового веса . Для целей анализа было использовано двунаправленное углеродное волокно — одно из них чаще всего используется для производства композитов, а одно-направленное углеродное волокно — иногда используется, в основном для изделий, где напряжение ожидается только в одной плоскости.
Анализ алюминия, стали и двунаправленного углеродного волокна на жесткость по отношению к весу и прочность по отношению к весу:
Алюминий | Сталь | Углеродное волокно в двух направлениях — общий модуль | Углеродное волокно с двумя направлениями — улучшенный модуль | Углеродное волокно в двух направлениях — максимальный модуль | |
Жесткость относительно веса (удельный модуль) | 26 | 25 | 56 | 83 | 120 |
Устойчивость к повреждениям (Удельная прочность) | 214 | 254 | 392 | 211 | 126 |
Анализ алюминия, стали и однонаправленного углеродного волокна на жесткость по отношению к весу и прочность по отношению к весу:
Алюминий | Сталь | Углеродное волокно в одном направлении — общий модуль | Углеродное волокно с односторонним направлением — улучшенный модуль | Углеродное волокно с односторонним направлением — максимальный модуль | |
Жесткость относительно веса (удельный модуль) | 26 | 25 | 113 | 166 | 240 |
Устойчивость к повреждениям (Удельная прочность) | 214 | 254 | 785 | 423 | 252 |
Приведенные выше данные для листов из углеродного волокна относятся к образцу, изготовленному с использованием технологии вливания эпоксидной смолы (соотношение углеродного волокна к смоле составляет 70/30%).
Приведенное выше утверждение демонстрирует множество преимуществ, которые дает углеродное волокно, а также элементы, разработанные и изготовленные из углеродного волокна. Ткани с улучшенным и самым высоким модулем относятся к специальным материалам (к сожалению, очень дорогостоящим), которые обладают характеристиками жесткости в 2 или 3 раза больше, чем стандартное углеродное волокно, и используются в основном в военных приложениях и в аэрокосмической промышленности.
Чтобы интерпретировать результаты, представленные в таблице, представьте, что инженер-конструктор собирается построить прочный и легкий лист из углеродного волокна толщиной 1 м. 2 с максимальным весом 10 кг. и он рассматривает алюминий, сталь и углеродное волокно.
Помня о предельном весе в 10 кг , инженер-конструктор может выбрать:
- Стальной лист толщиной около 1,5 мм.
- Лист алюминиевый около толщиной 4 мм.
- Углеродное волокно лист около толщиной 7 мм.
Углеродное волокно обеспечивает 2 важных преимущества.
Углеродное волокно обеспечивает большую жесткость (как описано выше) при более низкой плотности, и, следовательно, продукт того же веса может быть толще, что приведет к повышению жесткости только за счет увеличения толщины.Проще говоря, увеличение толщины материала в 2 раза обеспечивает жесткость 2 3 — то есть примерно в 8 раз больше. Это дает много возможностей для снижения веса за счет использования углеродного волокна.
2. Жесткость и прочность материала при одинаковой толщине стенки элемента
Очень часто инженеры-проектировщики ищут материал, который позволил бы им изготовить компонент, идентичный алюминиевому по всем размерам, включая толщину .В таблицах ниже показаны сравнения жесткости и прочности компонентов одинаковой толщины, изготовленных из алюминия, стали и углеродного волокна. Обратите внимание, что компонент из углеродного волокна тех же размеров будет на 42% легче алюминиевого и более чем в 5 раз легче стального. Подробнее читайте в разделе 3. Вес / плотность материала .
Жесткость и прочность при одинаковой толщине стенки: для алюминия, стали и двунаправленного углеродного волокна:
Алюминий | Сталь | Углеродное волокно в двух направлениях — общий модуль | Углеродное волокно с двумя направлениями — улучшенный модуль | Углеродное волокно в двух направлениях — максимальный модуль | |
Жесткость (модуль Юнга) Единица: ГПа | 69 | 200 | 90,5 | 132 | 190 |
Предел прочности (Предел прочности на разрыв — Предел прочности) Единица кН · м / кг | 500 | 1000 | 800 | 368 | 126 |
Жесткость и прочность при одинаковой толщине стенки: для алюминия, стали и однонаправленного углеродного волокна:
Материал | Алюминий | Сталь | Углеродное волокно в одном направлении — общий модуль | Углеродное волокно с односторонним направлением — улучшенный модуль | Углеродное волокно с односторонним направлением — максимальный модуль |
Жесткость (модуль Юнга) Единица: ГПа | 69 | 200 | 181 | 264 | 380 |
Предел прочности (Предел прочности при растяжении — Предел прочности ) Единица измерения кН · м / кг | 500 | 1000 | 1600 | 736 | 252 |
Компонент, сделанный из стандартного углеродного волокна той же толщины, что и алюминиевый, будет иметь на 31% большую жесткость, чем алюминиевый , и в то же время вес на 42% меньше и на 60% больше прочности.
Использование углеродного волокна с более высоким модулем и однонаправленной ткани может обеспечить в 4 раза большую жесткость по сравнению с алюминием при аналогичной или улучшенной предельной прочности.
Обратите внимание, что на практике сталь и алюминий имеют предел прочности ниже указанного в таблице.Это связано с тем, что до полного разрушения (расчет предела прочности был основан на этом моменте) металлический элемент подвергнется остаточной деформации (не восстановит свои первоначальные размеры).
Момент возникновения остаточного изгиба (без разрушения) относится к пределу текучести. Для устойчивости к повреждению в приведенных выше данных применяли предел прочности на разрыв, который относится к сопротивлению полному разрушению (растрескиванию).
Например, при гибке листового алюминия до полного разрушения и растрескивания образец сначала будет разрушен (без возможности восстановления исходных размеров).Данные, представленные в таблице, относятся к полностью разрушенным образцам (растрескиванию) с предположением, что изгиб приведет к полному разрушению (что не совсем правильно). Углеродное волокно имеет другие характеристики — в случае нагрузки, вызывающей постоянное изгибание алюминия без восстановления первоначальных размеров, углеродное волокно будет демонстрировать большую эластичность и после кратковременного изгиба восстановит свою форму после снятия нагрузки (эффект возврата пружины). Полное разрушение элемента из углеродного волокна произойдет внезапно и без какого-либо предупреждения — в отличие от алюминия, который имеет некоторые предупреждения, связанные с постоянным изгибом.Всегда помните вышесказанное при разработке компонента из углеродного волокна, чтобы предусмотреть некоторый допуск.
В ролике ниже сравнивается устойчивость к повреждениям карданного вала из углеродного волокна и стального, а также описывается процесс разрушения материала:
Что касается интерпретации результатов в таблице, очевидно, что углеродное волокно с наивысшим модулем упругости обеспечивает исключительную жесткость. Однако устойчивость к повреждениям уменьшается с увеличением жесткости (более высокий модуль).
Другой пример: лист из углеродного волокна с максимальной жесткостью, сделанный из тканей с наивысшим модулем упругости, будет иметь меньшую устойчивость к повреждениям. Чем больше компонент армирован тканями с наивысшим модулем упругости, тем больше он будет подвержен разрыву при изгибе.
Дальнейший анализ будет проводиться с углеродным волокном со стандартным модулем упругости, а композиты, изготовленные из тканей с наивысшим модулем упругости, предоставят возможности благодаря углеродным композитам.
Обратите внимание, что и алюминий, и углеродное волокно могут использоваться в качестве «гибридов», которые придают детали другие характеристики. В случае алюминия это относится к сплавам наряду с другими металлами, а в случае углеродного волокна — к одновременному использованию арамидных, стеклянных, базальтовых или вектроновых волокон.
Очень распространены композиты кевлар и арамид-кевлар-углерод, которые обеспечивают жесткость и высокую устойчивость к повреждениям. , но это будет предметом другого исследования.
3. Вес / плотность материала
Вес важен для многих продуктов.Например, снижает вес рычага / улавливателя автоматизированной машины для тяжелых условий эксплуатации, которая работает со скоростью 10 м / сек. позволит увеличить его скорость и продлить срок службы. В промышленных масштабах это может привести к увеличению производственных мощностей и значительной экономии.
Другим примером может быть инвалидная коляска, уменьшение веса которой позволяет легче подниматься в машину и выходить из нее, а также обеспечивает лучший контроль. Это очень очевидно в случае гоночных автомобилей Формулы 1, где замена алюминия углеродным волокном привела к снижению веса, что является критическим в этом виде спорта.
Автоматическая стрела KUKA, изготовленная из углеродного волокна, позволяет увеличить рабочую скорость и в то же время уменьшить ее вес, что приводит к снижению нагрузки на подшипники и другие детали, подверженные износу.Автоматическая стрела KUKA из углеродного волокна позволяет увеличить рабочую скорость и в то же время уменьшить ее вес, что приводит к уменьшению нагрузки на подшипники и другие детали, подверженные износу.
Из сравнения алюминия с углеродным волокном мы знаем, что плотность материала напрямую влияет на его вес.
Композиты из углеродного волокна имеют плотность 1,55 г / см 3 (эпоксидная смола 30%, углеродное волокно 70%), что в случае алюминия составляет 2,7 г / см 3 и 4,5 г / см 3 для титана или 7,9 г / см 3 для стали.
Композит из углеродного волокна имеет плотность почти в 2 раза меньше, чем у алюминия, и более чем в 5 раз меньше, чем у стали. Следовательно, в компоненте тех же размеров замена алюминия на углеродное волокно снизит его вес на ~ 42% . Замена стали на углеродное волокно уменьшит вес в 5 раз.
Чтобы проиллюстрировать это, представьте себе лист толщиной 6 мм и площадью 1 м 2 .
Один квадратный метр листа углеродного волокна толщиной 6 мм имеет вес:
- 47,4 кг для стального листа
- 16,2 кг для алюминиевого листа
- 9,3 кг для листа углеродного волокна.
При проектировании изделий и при выборе материала необходимо принимать во внимание жесткость, а также прочность данного материала, как описано в разделах 1 и 2 настоящего исследования. На практике возможности снижения веса компонентов за счет замены алюминия углеродным волокном потребовали дальнейших испытаний и экспериментов. Каждый элемент относится к индивидуальному случаю уникальной геометрии и параметров. Обычно можно снизить вес на 20-40%, используя углеродное волокно.
Кузов автомобиля из углеродного волокна позволил BMW снизить вес модели IS на 300 кг.BMW запустила производство полных кузовов из углеродного волокна для своей модели I3.Кузов машины из углеродного волокна позволил снизить вес каждой машины на 300 кг. Ежегодно компания производит десятки тысяч таких автомобилей. На самом деле эта модель интересует больше клиентов, чем первоначально прогнозировала BMW.
Уменьшение веса за счет использования углеродного волокна возможно и выгодно, особенно для продуктов, для которых значительна направленная сила. В отличие от металлов, композиты не демонстрируют одинаковой прочности в любом направлении (не однородны). Фактически именно во время производственного процесса принимаются решения относительно направления тканей (при использовании однонаправленных тканей) и направления, обеспечивающего наибольшую прочность за счет снижения прочности в других местах.Это решение позволяет еще больше снизить вес компонентов из углеродного волокна.
4. Обработка / резка
Углеродное волокно из-за своей низкой плотности является материалом, который легко обрабатывается станками с ЧПУ или ручными инструментами, включая угловую шлифовальную машину или дремель.
Углеродное волокно — это материал, который можно легко обработать на станке с ЧПУ — на фото показан тату-станок, сделанный из углеродного волокна.Хотя высококачественные конструкции из углеродного волокна, полученные вакуумным методом (наплавка смолы, препрег), могут иметь резьбу, там, где требуется много резьбовых соединений, вместо них используются специальные вставки.
Алюминиевые элементы соединяют чаще всего сваркой, клепкой или вставками. С углеродным волокном чаще всего применяется склейка, при необходимости с армирующими заклепками и вставками. Современные Эпоксидные клеи обеспечивают прочность склеивания, аналогичную сварке.
Интересно, что Ferrari постепенно внедряла новую технологию, которая заменила сварку алюминия склеиванием эпоксидным клеем . В настоящее время Ferrari 458 Italia имеет 70 м сварных швов и 8 м клея .Главный инженер Ferrari Moruzzi ожидает, что в будущем из-за изменения производственных процессов в кузовах автомобилей будет больше склеивания, чем сварки. Для Ferrari это возможность использовать другие алюминиевые сплавы, которые обладают улучшенными характеристиками, но не поддаются сварке.
Сравнивая склеивание со сваркой, обратите внимание, что склеивание требует простого внедрения технологии (хотя требуются ноу-хау и опыт).
Технология склеивания широко используется в авиационной промышленности для уменьшения веса и, в то же время, снижения расхода топлива.
Однако склеивание имеет некоторые недостатки, в том числе подготовку поверхности или время, необходимое для приклеивания клеевого покрытия. Во многих случаях компоненты, которые могут подвергнуться удару (например, в автомобильной аварии), усилены специальными вставками для противодействия внезапной разрывной нагрузке.
Технология склеиваниябудет использоваться чаще в связи с разработкой более мощных клеев и повышением осведомленности о ее преимуществах и возможных возможностях.
5.Тепловое расширение
Каждый материал имеет разные характеристики теплового расширения.
Тепловое расширение связано с изменением размеров материала из-за изменения температуры. Углеродное волокно на практике показывает почти нулевое тепловое расширение и поэтому широко используется в устройствах, включая 3D-сканеры.
Поскольку на практике углеродное волокно демонстрирует почти нулевое тепловое расширение, оно широко используется в устройствах, включая 3D-сканеры.Поскольку на практике углеродное волокно демонстрирует почти нулевое тепловое расширение, оно широко используется в устройствах, включая 3D-сканеры .
Инженеры-конструкторы все чаще убеждаются во многих преимуществах углеродного волокна благодаря низкому тепловому расширению по сравнению с традиционными материалами, такими как сталь или алюминий. Углеродное волокно демонстрирует исключительные параметры в этом отношении и подходит, в частности, для высокоточных элементов, таких как оптические устройства, 3D-сканеры, телескопы и другие, где крайне важно минимальное низкое тепловое расширение.
Углеродное волокно (композит из углеродного волокна и эпоксидной смолы) представляет собой материал с тепловым расширением в 6 раз меньше алюминия и более чем в 3 раза меньше стали.
В приведенной ниже таблице содержится анализ теплового расширения различных материалов с учетом соотношения дюйм / градус Фаренгейта. Указанные единицы предназначены только для справки в отношении различий между материалами.
Материал | Тепловое расширение |
Алюминий | 13 |
Сталь | 7 |
Стекловолокно — эпоксидный композит | 7-8 |
Кевлар / арамид — эпоксидный композит | 3 |
Углеродно-эпоксидный композит | 2 |
6.Теплопроводность
Углеродное волокно — это материал с низкими характеристиками теплопроводности.
Углеродное волокно — идеальный изолятор — на фотографии выше показан вход турбины из углеродного волокна.Теплопроводность в основном зависит от передачи / проводимости энергии из областей с высокой температурой в области с низкой температурой. Материалы с высокой теплопроводностью переносят температуру легче, чем материалы с низкой теплопроводностью.
Композит из углеродного волокна и эпоксидной смолы — это материал с теплопроводностью в 40 раз меньше, чем у алюминия, и в 10 раз меньше, чем у стали. Следовательно, можно предположить, что углеродное волокно является очень хорошим изолятором.
В этой таблице сравнивается теплопроводность различных материалов, включая углеродное волокно (единица измерения Вт / м *)
Материал | Теплопроводность |
Углеродно-эпоксидный композит | 5-7 |
Сталь | 50 |
Алюминий | 210 |
7.Устойчивость к температуре
Алюминий — это материал, устойчивый к высоким температурам, и в этом отношении он имеет преимущества перед композитами из углеродного волокна.
Характеристики и устойчивость углеродного волокна к высоким температурам зависят от структуры композита и технологии выпечки. Это правда, что композит из углеродного волокна устойчив к высоким температурам , но, к сожалению, часто это не так. На самом деле это происходит из-за использования неподходящих материалов, неправильного обжига композита или недостаточного ноу-хау и опыта в этом отношении многих поставщиков композитов.
Для обеспечения устойчивости к высоким температурам во время производства могут использоваться только материалы, демонстрирующие такую стойкость, при условии, что обжиг композита выполняется надлежащим образом в диапазоне температур, близком к желаемой стойкости композита. Использование смол, устойчивых к высоким температурам, без дополнительного отверждения внутри духовки не обеспечит требуемой стойкости.
Стандартные эпоксидные композиты из углеродного волокна, прошедшие надлежащую термостойкость при температуре до 70–100 ° C (160–210 ° F).
Если требуется устойчивость к температурам выше 100 ° C, чаще всего подходит препрег из углеродного волокна , часто вместе с упрочнением композита при температурах около 150 ° C / 300 ° F, что позволяет повысить стойкость до температур 200 ° C / 400 ° F. Например, Prepreg Gurit EP127 обладает стойкостью до 230 ° C / 445 ° F.
Если требуется устойчивость к более высоким температурам, используются фенольные смолы, и эти композиты обладают кратковременной стойкостью до 500 ° C / 930 ° F.
Хотя такое сопротивление может быть обеспечено для композитов, обратите внимание, что эти специальные материалы дороги и требуют не только закалки в печи при высокой температуре, но и ноу-хау. Поэтому все это приводит к высокой цене на композиты, устойчивые к очень высоким температурам.
8. Долгосрочная работа
Углеродный композит при строительстве должен изготавливаться вакуумным методом — настаиванием смолы или препрега.Такая технология обеспечивает долгий срок службы углеродного композита. Углеродный композит, изготовленный вручную «валиком и кистью», имеет низкую прочность и небольшой срок службы.
Углеродное волокно обладает стойкостью к коррозии, что дает еще одно преимущество по сравнению с алюминием.
Углеродно-эпоксидный композит имеет недостаток, связанный с пониженной стойкостью к УФ-излучению, поэтому композит, подвергающийся воздействию УФ-излучения, следует защищать путем нанесения верхнего покрытия, что в качестве дополнительного процесса приводит к более высоким производственным затратам.
9. Внедрение производства
Почему углеродное волокно не широко используется в производственных циклах, хотя оно имеет много преимуществ по сравнению с очень популярным алюминием?
Чаще всего это связано с ценой: элементы из углеродного волокна стоят дороже алюминиевых, потому что углеродное волокно стоит дороже, а производство углеродных изделий требует больше времени.
С другой стороны, при сравнении затрат, связанных с реализацией производства алюминия и углеродного волокна, во многих случаях именно производство элемента из углеродного волокна будет дешевле и, что более важно, доступно в случае небольшого тиража, для которого внедрение производства алюминиевых элементов было бы нерентабельным.
В следующем фильме показано производство элементов из углеродного волокна с использованием технологии препрега.
Наконец, мы должны упомянуть широко распространенное непонимание преимуществ и преимуществ углеродного волокна по сравнению с традиционными материалами, включая алюминий или сталь. Мы надеемся, что эта статья дает больше информации об углеродном волокне и о том, чем этот материал отличается от алюминия, а также о том, какие преимущества возможны при замене алюминия углеродным волокном.
10. Резюме
Мы надеемся, что это исследование предоставило больше информации о свойствах углеродного волокна по сравнению с алюминием. Со временем все больше и больше инженеров-конструкторов будут использовать этот материал, поскольку углеродное волокно предлагает множество преимуществ, включая легкий вес, практически нулевое тепловое расширение, простоту обработки и высокую жесткость.